Сварочная проволока для сварки стали 12х18н10т

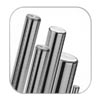
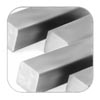
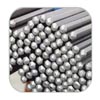


Продажа нержавейки со склада в Москве и под заказ.
О компании | Каталог | Спецпредложения | Отправить запрос | Справочник | Цены |
![]() |
ГОСТ |
Марочник |
Применение |
Статьи |

12Х18Н10Т. Особенности сварки нержавейки.
Сварка стали – основной технологический процесс практически любого производства изделий из металла. С VII века до нашей эры и до наших дней сварка широко применяется как основной способ образования неразъемных соединений металлов. С самого зарождения и вплоть до XIX века н.э. в применялся метод кузнечной сварки металлов. Т.е. свариваемые детали нагревались и затем спрессовывались ударами молота. Эта технология достигла своего пика к середине XIX века, когда по ней стали изготавливать даже такие ответственные изделия как железнодорожные рельсы и магистральные трубопроводы.
Однако сварные соединения, особенно в массовом, промышленном масштабе отличались невысокой надежностью и нестабильным качеством. Это зачастую приводило к авариям из-за разрушения детали в месте шва.
Открытие электродугового нагрева и высокотемпературного газо-кислородного горения наряду с возросшими требованиями к качеству сварного соединения совершили мощный технологический прорыв в области сварки, в результате чего создалась технология бескузнечной сварки — такой, какую мы привыкли наблюдать сегодня.
С появлением легированной стали процессы сварки усложнились в связи с необходимостью предотвращения карбидации легирующих элементов, в основном – хрома. Появились методы сварки в инертных средах или под флюсом, а также технологии долегирования сварного шва.
Рассмотрим особенности сварки аустенитных сталей на примете наиболее распространенной нержавеющей стали 12Х18Н10Т.
Сталь 12Х18Н10Т относиться к хорошо свариваемым. Характерной особенностью сварки этой стали является возникновение межкристаллитной коррозии. Она развивается в зоне термического влияния при температуре 500-800?С. При пребывании металла в таком критическом интервале температур по границам зерен аустенита выпадают карбиды хрома. Все это может иметь опасные последствия — хрупкие разрушения конструкции в процессе эксплуатации.
Чтобы добиться стойкости стали нужно исключить или ослабить эффект выпадения карбидов и стабилизировать свойства стали в месте сварного шва.
При сварке высоколегированных сталей используют электроды с защитно-легирующим покрытием основного вида в сочетании с высоколегированным электродным стержнем. Применение электродов с покрытием основного вида позволяет обеспечить формирование наплавленного металла необходимого химического состава, а также других свойств путём использования высоколегированной электродной проволоки и долегирования через покрытие.
Сочетание легирования через электродную проволоку и покрытие позволяет обеспечить не только гарантированный химический состав в пределах паспортных данных, но и некоторые другие свойства, предназначенные для сварки аустенитных сталей 12Х18Н10Т, 12Х18Н9Т, 12Х18Н12Т и им подобных.
Содержащийся в электродных стержнях титан при сварке практически полностью окисляется. По этой причине при сварке покрытыми электродами в качестве элемента-стабилизатора используют ниобий. Коэффициент перехода ниобия из стержня при сварке покрытыми электродами составляет 60-65%.
Сварку высоколегированных сталей под флюсом осуществляют с применением или нейтральных по кислороду фторидных флюсов, или защитно-легирующих в сочетании с высоколегированной электродной проволокой. С металлургической точки зрения для сварки высоколегированных сталей наиболее рациональны фторидные флюсы типа АНФ-5, которые обеспечивают хорошую защиту и металлургическую обработку металла сварочной ванны и позволяет легировать сварочную ванну титаном через электродную проволоку. При этом процесс сварки малочувствителен к образованию пор в металле шва из-за водорода. Однако фторидные бескислородные флюсы имеют относительно низкие технологические свойства. Именно низкие технологические свойства фторидных флюсов служат причиной широкого использования для сварки высоколегированных сталей флюсов на основе оксидов.
Сварку высоколегированных сталей для снижения вероятности формирования структуры перегрева, как правило, выполняют на режимах, характеризующихся малой величиной погонной энергии. При этом предпочтение отдают швам малого сечения, получаемым при использовании электродной проволоки небольшого диаметра (2-3мм). Поскольку высоколегированные стали обладают повышенным электросопротивлением и пониженной электропроводностью, то при сварке вылет электрода из высоколегированной стали уменьшают в 1,5-2 раза по сравнению с вылетом электрода из углеродистой стали.
При дуговой сварке в качестве защитных газов используют аргон, гелий (реже), углекислый газ.
Аргонодуговую сварку выполняют плавящимися и неплавящимися вольфрамовыми электродами. Плавящимся электродом сваривают на постоянном токе обратной полярности, используя режимы, обеспечивающие струйный перенос электродного металла. В некоторых случаях (в основном при сварке аустенитных сталей) для повышения стабильности горения дуги и особенно снижения вероятности образования пор из-за водорода при сварке плавящимся электродом используют смеси аргона с кислородом или углекислым газом (до 10%).
Сварку неплавящимся вольфрамовым электродом в основном осуществляют на постоянном токе прямой полярности. В некоторых случаях при наличии в сталях значительного количества алюминия используют переменный ток для обеспечения катодного разрушения оксидной плёнки.
Применение дуговой сварки в атмосфере углекислого газа позволяет снизить вероятность образования пор в металле шва из-за водорода; при этом обеспечивается относительно высокий коэффициент перехода легкоокисляющихся элементов. Так, коэффициент перехода титана из проволоки достигает 50%. При сварке в атмосфере аргона коэффициент перехода титана из проволоки составляет 80-90%. При сварке в углекислом газе сталей, имеющих высокое содержание хрома и низкое содержание кремния, на поверхности шва образуется тугоплавкая трудноудаляемая оксидная плёнка. Её присутствие затрудняет проведение многослойной сварки.
При сварке сталей с малым содержанием углерода (ниже 0,07-0,08%) возможно науглероживание наплавленного металла. Переход углерода в сварочную ванну усиливается при наличии в электродной проволоке алюминия, титана, кремния. В случае сварки глубокоаустенитных сталей некоторое науглероживание металла сварочной ванны в сочетании с окислением кремния снижает вероятность образования горячих трещин. Однако науглероживание может изменить свойства металла шва и, в частности, снизить коррозийные свойства. Кроме того наблюдается повышенное разбрызгивание электродного металла. Наличие брызг на поверхности металла снижает коррозийную стойкость.
Технологии сварки нержавеющих высоколегированных сталей постоянно совершенствуются. На данном этапе при строгом соблюдении технологического процесса качество сварного шва нержавейки практически не уступает по своим свойствам металлу соединяемых деталей и гарантирует высочайшую надежность сварного соединения.
Посмотреть специальные предложения на продажу стали 12Х18Н10Т.
В данной статье рассмотрим технологию сварки некоторых легированных хромоникелевых аустенитных сталей, а именно:
— коррозионно-стойких сталей (они же нержавеющие или попросту "нержавейка");
— жаропрочных и жаростойких сталей.
Технология сварки хромоникелевых аустенитных сталей . Все заготовительные операции на аустенитных сталях, выполняемые методами холодной или горячей обработки, производятся в основном теми же способами и на том же оборудовании, что и для углеродистых конструкционных сталей. Подготовка кромок деталей под сварку должна производиться механическим путем (фрезерованием, строжкой, токарной обработкой). Допускается подготовка кромок сжатой дугой или газофлюсовой резкой, требующей последующей механической зачистки огнерезных кромок на глубину не менее 0,8 мм.
При сборке деталей перед прихваткой и сваркой во избежание образования надрезов и трещин на поверхности основного металла в месте попадания брызг расплавленного металла участки рядом со швом должны быть покрыты одним из видов защитных покрытий.
При изготовлении сварных конструкций из аустенитных сталей могут применяться все способы электрической сварки плавлением. Выбор способа сварки производится с учетом толщины свариваемого металла, размеров и формы конструкции, расположения швов в пространстве и их доступности, требований к сварным соединениям и т. д.
Основной особенностью ручной дуговой сварки аустенитных сталей является необходимость обеспечения требуемого химического состава металла шва при различных типах сварных соединений и пространственных положениях сварки с учетом изменения доли участия основного и электродного металла в металле шва. Это заставляет корректировать состав покрытия с целью обеспечения необходимого содержания в шве феррита и тем самым предупреждения образования в шве горячих трещин. Этим же достигается и необходимая жаропрочность и коррозионная стойкость швов.
Применением электродов с фтористокальциевым покрытием, уменьшающим угар легирующих элементов, достигается получение металла шва с необходимым химическим составом и структурами. Уменьшению угара легирующих элементов способствует и поддержание короткой дуги без поперечных колебаний электрода. Последнее уменьшает и вероятность образования дефектов на поверхности основного металла в результате прилипания брызг.
Состав покрытия электрода определяет необходимость применения постоянного тока обратной полярности (при переменном токе или постоянном токе прямой полярности дуга неустойчива), величину которого определяют по формуле Iсв=kdэ, а коэффициент k в зависимости от диаметра электрода принимают не более 25-30 А/мм. В потолочном и вертикальных положениях силу сварочного тока умень¬шают на 10-30 % по сравнению с силой тока, выбранной для нижнего положения сварки.
Сварку покрытыми электродами рекомендуется выполнять валиками малого сечения и для повышения стойкости против горячих трещин применять электроды диаметром 3 мм с минимальным проплавлением основного металла. Тщательная прокалка электродов перед сваркой, режим которой определяется их маркой, способствует уменьшению вероятности образования в швах пор и трещин, вызываемых водородом. Некоторые марки электродов, рекомендуемые для различных сталей аустенитного класса, в зависимости от условий работы конструкции приведены в табл.1, а их механические свойства — в табл.2.
Таблица 1. Некоторые марки электродов и условия работы высоколегированных сталей и сплавов
08Х22Н6Т
Э 07Х20Н9
Э-08Х19Н10Г2Б
Э-02Х10Н9Б
10Х17НИМ2Т
08Х18Н19Б
08Х21Н6М2Т
Э-09Х19Н10Г2М2Б
20Х20Х14С2
20Х25Н20С2
30Х18Н25С2
3-10 %
Аустенитно-
карбидная
Таблица 2. Типичные механические свойства при температуре 20 о С металла швов, выполненных на высоколегированных коррозионно-стойких и жаропрочных сталях |
Марка электрода |
σт | σв | δ, % | KCU, Дж/см 3 |
МПа/м м 2 | ||||
Коррозионно-стойкие стали | ||||
ЦЛ-11 | 360 | 600 | 24 | 70 |
ОЗЛ-7 | 400 | 640 | 25 | 100 |
Л-38М | 300 | 600 | 30 | 90 |
СЛ-28 | — | 600 | 38 | 120 |
11Ж-13 | 450 | 600 | 26 | 100 |
Жаропрочные стали | ||||
ОЗЛ-5 | 350 | 600 | 25 | 60 |
ОЗЛ-6 | 350 | 570 | 33 | 100 |
ОЗЛ-9-1 | 500 | 650 | 12 | 50 |
Одним из основных способов сварки высоколегированных сталей толщиной 3-50 мм, применяемых в химической, нефтехимической аппаратуре, атомной технике и некоторых других отраслях промышленности является сварка под флюсом. Она имеет большое преимущество перед ручной дуговой сваркой покрытыми электродами ввиду стабильности состава и свойств металла по всей длине шва, при сварке с разделкой и без разделки кромок. Это достигается отсутствием частых кратеров, образующихся при смене электрода, обрывов дуги, равномерностью плавления электродной проволоки и основного металла по длине шва (при ручной сварке в связи с изменением вылета электрода скорость его плавления вначале будет меньше, чем в конце, что периодически изменяет долю основного металла в шве, а значит и его состав) и более надежной защитой зоны сварки от окисления легирующих компонентов кислородом воздуха.
Хорошее формирование поверхности швов с мелкой чешуйчатостью и плавным переходом к основному металлу, отсутствие брызг на поверхности изделия заметно повышают коррозионную стойкость сварных соединений. При этом способе уменьшается трудоемкость подготовительных работ, так как разделку кромок производят на металле толщиной выше 12 мм (при ручной сварке свыше 3-5 мм). Возможна сварка с повышенным зазором и без разделки кромок стали толщиной до 30-40 мм. Уменьшение потерь на угар, разбрызгивание и огарки электродов на 10-20 % снижает расход дорогостоящей сварочной проволоки.
При сварке под флюсом значительно труднее обеспечить необходимое содержание ферритной фазы в металле шва только за счет выбора сварочных флюсов и проволок, которые в пределах одной марки имеют значительные колебания химического состава. На содержание ферритной фазы в металле влияет также его толщина и разные формы разделки, приводящие к изменению доли участия основного металла в металле шва. Техника и режимы сварки под флюсом высоколегированных сталей отличаются от сварки обычных низколегированных.
Для предупреждения перегрева металла и связанного с этим укрупнения структуры, возможности появления трещин и снижения эксплуатационных свойств сварного соединения рекомендуется выполнять сварку валиками небольшого сечения, применяя для этого проволоку диаметром 2- 3 мм, а в связи с высоким электросопротивлением аустенитных сталей вылет электрода следует уменьшить в 1,5-2 раза.
Легировать шов можно через флюс (табл. 3) или проволоку (табл. 4), последнее предпочтительнее, так как обеспечивает необходимую стабильность металла шва.
Таблица 3. Флюсы для электродуговой и влектрошлаковой сварки высоколегированных сталей
Вид сварки
Марка флюса
Автоматическая электродуговая аустенитно-ферритными швами
АНФ-14; АНФ-16; 48-ОФ-Ю; К-8
Автоматическая электродуговая аустенитно-ферритными швами с небольшим запасом аустенита
Автоматическая электродуговая чисто аусте-нитными швами с большим запасом аустенита
Автоматическая электродуговая и электрошлаковая чисто аустенитными швами с большим запасом аустенита
Электрошлаковая чисто аустенитными швами с большим запасом аустенита
АНФ-1; АНФ-6; АНФ-7; АН-29; АН-292
Таблица 4. Некоторые марки сварочной проволоки для электродуговой сварки под флюсом и электрошлаковой сварки высоколегированных сталей
Марка стали
Условия работы
Марка проволоки
(ГОСТ 2246 — 70)
12Х18Н9
08Х18Н10
12Х18Н10Т
12Х18Н9Т
Стойкость к межкристаллитной коррозии
Св-0,4Х19Н9
Св-07Х18Н9ТЮ
Св-04Х19Н9С2
Св-05Х19Н9ФЗС2
12Х18Н10Т
08Х18Н10Т
08Х18Н12Т
08Х18Н12Б
Температура выше 350°С;
стойкость к межкристаллитной коррозии
Стойкость к межкри-сталлитной коррозии
08Х18Н10;
12Х18Н10Т
12Х18Н9Т
Сварка в углекислом газе; стойкость к межкристаллитной коррозии
Температура до 800- 900 °С
20Х23Н13
08Х20Н14С2
20Х23Н18
Температура 800-900 °С
Температура 900- 1100°С
Температура до 1200°С
Св-07Х25Н12Г2Т
Св-06Х25Н12ТЮ
Св-08Х25Н13БТЮ
Д ля сварки используют низкокремнистые фторидные флюсы, создающие в зоне сварки безокислительные или малоокислительные среды, что приводит к минимальному угару легирующих элементов. Для снижения вероятности образования пор в швах флюсы для высоколегированных сталей необходимо прокалить непосредственно перед сваркой при 500-800°С в течение 1-2 ч. Остатки шлака и флюса на поверхности швов, которые могут служить очагами коррозии сварных соединений на коррозионно-и жаростойких сталях, необходимо тщательно удалять.
Особенностью электрошлаковой сварки является пониженная чувствительность к образованию горячих трещин, что объясняется малой скоростью перемещения источника нагрева и характером кристаллизации металла сварочной ванны, в результате создаются условия получения чисто аустенитных швов без трещин. Однако длительное пребывание металла шва и околошовной зоны при повышенных температурах увеличивает его перегрев и ширину околошовной зоны, а длительное пребывание металла при температурах 1200-1250°С приводит к изменению его структуры, снижает прочностные и пластические свойства. В результате сварные соединения теплоустойчивых сталей предрасположены к разрушениям в процессе термической обработки или эксплуатации при повышенных температурах.
Перегрев при сварке зоны термического влияния коррозионно-стойких сталей может привести к образованию в ней ножевой коррозии, поэтому для предупреждения указанных дефектов необходима термообработка сварных изделий (закалка или стабилизирующий отжиг). При выборе флюса и сварочной проволоки необходимо учитывать проникновение кислорода воздуха через поверхность шлаковой ванны, что приводит к угару легкоокисляющихся элементов (титана, марганца и др.). Это вызывает необходимость в некоторых случаях защищать поверхность шлаковой ванны путем обдува аргоном.
Электрошлаковую сварку высоколегированных сталей можно выполнять проволочным или пластинчатыми электродами (табл. 5). Изделия большой толщины со швами небольшой протяженности целесообразно сваривать пластинчатым электродом, изготавливать их значительно проще. Но сварка проволокой позволяет в широких пределах, варьируя режимом, изменять форму металлической ванны и характер кристаллизации шва, а это является одним из действенных факторов, обеспечивающих получение швов без горячих трещин.
Таблица 5. Типовой режим электрошлаковой сварки высоколегированных сталей и сплавов
Толщина
металла,
мм
Электрод
Диаметр,(размеры),
мм
Марка флюса
Зазор, мм
Скорость
подачи
электрода,
м/ч
Сила
сварочного
тока,
А
Напряжение, В
Глубина шлаковой ванны, мм
АНФ-7 АНФ-7 АНФ-1 АНФ-6
28-32 28-32 38-40 38-40
600-800 1200-1300 3500-4000 1800-2000
24-26
22-24
26-28
Однако жесткость сварочной проволоки затрудняет длительную и надежную работу токоподводящих и пода¬ющих узлов сварочной аппаратуры.
При сварке в углекислом газе создается окислительная атмосфера в дуге за счет диссоциации углекислого газа, вызывающая повышенное (до 50 %) выгорание титана и алюминия. Меньше выгорают марганец, кремний и другие легирующие элементы, поэтому при сварке коррозионно-стойких сталей в углекислом газе применяют сварочные проволоки, содержащие раскисляющие и карбидообразующие элементы (алюминий, титан, ниобий). Недостатком сварки в углекислом газе является интенсивное разбрызгивание металла и образование на поверхности шва плотных пленок оксидов, прочно сцепленных с металлом, что может снизить коррозионную стойкость и жаростойкость сварного соединения.
Для уменьшения налипания брызг на основной металл наносят эмульсии, а для борьбы с оксидной пленкой подается в дугу небольшое количество фторидного флюса АНФ-5.
Сварка плавящимся электродом в углекислом газе производится на полуавтоматах и автоматах. При этом для сварки сталей марки 12Х18Н10Т рекомендуется проволока Св-07Х18Н9ТЮ, Св-08Х20Н9С2БТЮ; для сталей марки 12Х18Н12Т — проволока Св-Х25Н13БТЮ, а для хромоникелемолибденовых сталей — проволока марок Св-06Х19Н10МЗТ и Св-06Х20Н11МЗТБ. Сварка в углекислом газе производится во всех пространственных положениях, что позволяет механизировать сварочные работы на конструкциях из высоколегированных сталей в монтажных условиях.
Ориентировочные режимы дуговой сварки в углекислом газе высоколегированных сталей без разделки кромок плавящимся электродом в углекислом газе приведены в табл. 6.
Таблица 6. Режимы дуговой сварки высоколегированных сталей без разделки кромок плавящимся электродом в углекислом газе
Шов
Диаметр
проволоки,
мм
Напряжение дуги, В
Расход
углекислого
газа,
л/мин
80 230-240
250-260
350-360
380-400
430-450
530-560
При сварке в инертных газах повышается стабильность дуги и снижается угар легирующих элементов, что важно при сварке высоколегированных сталей.
Сварку аустенитных сталей в инертных газах выполняют неплавящимся (вольфрамовым) или плавящимся электродом. Обычно ее применяют для сварки материала толщиной до 7 мм, но особо эффективна она при малых толщинах (до 1,5 мм), когда при применении других способов наблюдаются прожоги. Однако в некоторых случаях ее применяют при сварке неповоротных стыковых труб большой толщины, и сварке корневых швов в разделке при изготовлении особо ответственных толстостенных изделий. Сварку ведут без присадочного материала или с присадочным материалом на постоянном токе прямой полярности. Но при сварке стали или сплава с повышенным содержанием алюминия применяют переменный ток, чтобы за счет катодного распыления разрушить поверхностную пленку оксидов.
Плазменная сварка также используется для высоколегированных сталей. Ее преимуществами являются чрезвычайно малый расход защитного газа, возможность получения плазменных струй различного сечения (круглого, прямоугольного, эллипсовидного и т. д.). Ее можно использовать для сварки очень малых толщин металла и для металла толщиной до 12 мм. Примерные режимы сварки высоколегированных сталей вольфрамовым электродом на постоянном токе обратной полярности присадочной проволокой диаметром 1,6 — 2,0 мм приведены в табл. 7.
Таблица 7. Режимы сварки вольфрамовым электродом в аргоне высоколегированных сталей
Толщина
металла,
мм
Тип соединения
Сила
сварочного
тока,
А
Расход аргона,
л/мин
Одну и ту же марку высоколегированных аустенитных сталей можно использовать для изготовления изделий различного назначения, например, коррозионно-стойких, хладостойких или жаропрочных. А вот требования к свойствам сварных соединений будут различными, что определит и различную технологию сварки (сварочные материалы, режимы сварки, необходимость последующей термообработки), направленную на получение сварного соединения с необходимыми свойствами, которые определяются составом металла шва и его структурой.
Пониженный коэффициент теплопроводности при равных прочих условиях изменяет распределение температур в шве и околошовной зоне. Поэтому одинаковые изотермы в высоколегированных сталях сильнее развиты, чем в углеродистых. Так увеличивается глубина проплавления основного металла, возрастает коробление изделий.
С целью уменьшения коробления изделий из высоколегированных сталей требуется применять способы и режимы сварки, которым свойственна максимальная концентрация тепловой энергии. Более высокое ( в 5 раз выше, чем у углеродистых сталей) удельное электросопротивление обусловливает больший разогрев сварочной проволоки в вылете электрода или металлического стержня электрода для ручной дуговой сварки. В процессе автоматической и полуавтоматической дуговой сварки следует уменьшать вылет электрода и повышать скорость его подачи. При ручной дуговой сварке уменьшают длину электродов для высоколегированных сталей и допустимую плотность сварочного тока.
Электроды с фтористокальциевым покрытием уменьшают угар легирующих элементов, значит, позволяют получить металл шва с необходимым химическим составом и структурами. Уменьшению угара легирующих элементов способствует и поддержание короткой дуги без поперечных колебаний электрода. Вероятность появления дефектов на поверхности основного металла в результате попадания на него брызг также снижается..
Ориентировочные режимы ручной дуговой сварки аустенитных сталей
Толщина материала,
мм
Электрод
Сила сварочного тока (А) при положении сварки
Некоторые марки электродов для сварки высоколегированных сталей и сплавов
Марка стали | Марка электродов | Тип электродов по ГОСТ 10052-75 | Структура наплавленного металла |
Коррозионно-стойкие стали
08Н18Н10,08Х18Н10Т, 12Х18Н10Т, 08Х18Н12Т, 08Х18Н12Б, 08Х22Н6Т и подобные, работающие в агрессивных средах:
к металлу шва предъявляются требования по стойкости к МКК
к металлу шва предъявляются жесткие требования по стойкости к МКК
10Х17Н13М2Т, 10Х17Н13МЗТ, 08Х18Н12Б, 08X2IH6M2T и подобные, работающие при температурах до 700 °С:
к металлу шва предъявляются требования по стойкости к МКК
к металлу шва предъявляются жесткие требования по стойкости к МКК
Жаропрочные стали
Жаростойкие стали
Типичные механические свойства металла шва при комнатной температуре
Марка электрода | σт, МПа | σв, МПа | δ, % | Ударная вязкость, Дж/см2 |
Коррозионно-стойкие стали
Жаростойкие стали
Сварка под флюсом
Этот способ сварки высоколегированных сталей толщиной 3 — 50 мм имеет некоторые преимущества перед ручной дуговой сваркой покрытыми электродами по нержавейке. Стабильность состава и свойств металла по всей длине шва при сварке с разделкой и без разделки кромок обеспечивает более высокое качество сварного соединения.
Флюсы для электродуговой и электрошлаковой сварки высоколегированных сталей
Марка флюса | Назначение |
АНФ-14; АНФ-16; |
Некоторые марки сварочных проволок для электродуговой сварки под флюсом и электрошлаковой сварки высоколегированных сталей
Марка стали | Марка проволоки |
Коррозионно-стойкие стали
Жаропрочные стали
Жаростойкие стали
Кратковременные механические свойства при температуре 20 °С металла шва и сварного соединения высоколегированных сталей и сплавов
Марка металла | Толщина, мм | Марка проволоки | Сварка | Испытуемый образец | σт, МПа | σв, МПа | δ, % |
*Термообработка: аустенизация при 1080 °С 2 ч на воздухе и старение при 700 °С 16 ч.
**Термообработка: старение при 800 °С 10 ч.
Электрошлаковая сварка.
Важнейшая отличительная особенность такого способа — пониженная чувствительность к образованию горячих трещин, позволяющая получать чисто аустенитные швы без трещин.
Длительная прочность сварных соединений высоколегированных сталей и сплавов
Марка металла
Сварка
Марка проволоки
Условия испытания
°С
В углекислом газе
В углекислом газе
В углекислом газе
** Термообработка: аустенизация при 1050 °С 15 мин и старение при 700 °С 16 ч.
Типовой режим электрошлаковой сварки высоколегированных сталей и сплавов
Сварка в защитных газах.
В качестве защитных газов используются как инертные (аргон, гелий), так и активные (углекислый), а также различные их смеси. Преимущества: можно использовать для соединения металлов широкого диапазона толщин (от десятых долей до десятков миллиметров). При сварке толстых металлов в некоторых случаях этот способ сварки может конкурировать с электрошлаковой сваркой.
Для высоколегированных сталей применяется и плазменная сварка.
Главное преимущество — малый расход защитного газа. Получение плазменных струй различного сечения (круглого, прямоугольного) и значительное изменение расстояния от плазменной горелки до изделия расширяют технологические возможности этого способа. Плазменную сварку можно использовать для очень тонких металлов и для металла толщиной до 12 мм. Применение ее для соединения сталей большой толщины затруднено опасностью образования в швах подрезов.
Примерные режимы аргонодуговой сварки вольфрамовым электродом высоколегированных сталей
«>
Отправить ответ