Плазморез с дежурной дугой
Содержание:
Автор: pnp_machinist, pnp_mechanic@mail.ru
Опубликовано 19.09.2016.
Создано при помощи КотоРед.
Простой аппарат плазменной резки.
Значение аппарата плазменной резки для народного хозяйства трудно переоценить. Так например одна только экономия металла при раскрое составляет 10-15%. Не говоря уже о возможности вырезать отверстия и детали различной формы в листовом металле. Появление на рынке сварочных инверторов и расходных материалов для плазмотронов сделало этот способ обработки металла доступным для широких масс населения.
В нашем случае в качестве рабочей среды плазмы используется осушенный атмосферный воздух давлением 3.5 – 4 Атм. Плазматрон CUT-40 как один из самых доступных . И инвертор сварочного тока выходным напряжением 100-140 вольт, 10-40 А. Этого вполне хватает для резки металла толщиной 0,5 – 6 мм. Исходя из данных — сила тока для реза 1 мм. толщины металла должна быть примерно 6 А
Теория.
Как видно на условном изображения горелки, атмосферный воздух одновременно является рабочей средой для образования плазмы и охлаждает элементы горелки.
В первый момент дуга разжигается высоковольтным разрядом между электродом и соплом при условии контакта последнего с анодом т.е. металлом. Далее образовавшаяся плазма выдувается потоком воздуха. Для поддержания стабильной дуги необходимо выдерживать зазор между соплом горелки и металлом около 1 мм. , что весьма трудно. Для этого предлагаются специальные насадки. Но как утверждают специалисты они только мешают. Я полностью разделяю их мнение и поэтому просто веду без нажима соплом горелки по заготовке. Замечено при недостаточном токе сопло "прилипает" к металлу. О успешном процессе резки можно судить по видимым искрам с обратной стороны металла. По окончании резки не следует отводить горелку, лучше прервать процесс снятием напряжения. Так продлевается срок службы электрода со вставкой из гафния .
Инвертор
Для силовой части хорошо подходит схема инвертора AVT-200. Данный инвертор уже неоднократно повторялся и хорошо известен в сети Интернет. Оригинал статьи автора доступен в архиве AVT-200.rar. Изменения коснулись узла формирования пилообразного напряжения на токовом входе компаратора и цепей задания тока. Изменена печатная плата.
Узел задания тока питается стабильным напряжением 15 В, что улучшает повторяемость. Для снижения уровня помех в цепях токового компаратора установлен резистор R90. Большая индуктивность выходного дросселя позволяет упростить схему формирования "пилы". В остальном схема мало отличается от оригинала. Для токового шунта необходимо использовать манганиновую проволоку. В моём случае при диаметре 0.9 мм длинна шунта 20 мм.
Отдельно отмечу в схеме отсутствует узел защиты от превышения тока и К.З. в нагрузке. Разумеется такие узлы необходимы. Но короткое замыкание в правильно собранной горелке CUT-40 не возможно. Если конечно сопло совсем расплавится и останется только электрод.
В большинстве случаев для успешного розжига плазмы хватает высоковольтного разряда напряжением 20-22 кВ. постоянного тока. Схема с искровым разрядником самая простая в реализации . Для снижения требований к повышающему трансформатору используется умножитель напряжения . Разрядник изготовлен из контактов реле , зазор 1 – 1.5 мм. Высоковольтный трансформатор намотан на ферритовом сердечнике диаметром 8 мм. длинной 80 мм Первичная обмотка 7-8 витков проводом МГТФ-0,35. Вторичная медным проводом ПЭВ- 2 диаметром 1,5 мм. Пропитан эпоксидной смолой. Между обмоточками изоляция обязательна. Накопительный конденсатора взят из стартёра времён СССР для лампы дневного света мощностью 80 Вт. Как оказалось другие конденсаторы — 10n 6,3 kV. сгорают после 3-й попытки розжига.
Схема управления.
Для работы реализована простая последовательность управления.
При нажатии кнопки оператора S3 последовательно происходит
1- Подача воздуха.
2- Пауза 0.5-1 сек. (это время необходимо для продувки плазмотрона)
3- Включение инвертора.
4- Включение осциллятора на 2 сек.
При размыкании кнопки выключается инвертор и с задержкой 3-4 сек. снимается напряжение с воздушного клапана. Этого времени достаточно для остывания горелки.
В исходном состоянии все реле обесточены и копка оператора S3 отжата. При замыкании S3 сработает реле REL 2 и своими контактами замкнёт базовые цепи транзисторов Т1, Т3, Т4, Т6. к общему проводу. Причём напряжение на базе транзисторе Т1 появится с небольшой задержкой обусловленной RC цепочкой R4,C1. Стабилитрон в цепи коллектора Т1 определяет пороговое напряжение при открытии транзистора, что также является своеобразной защитой от помех в цепях управления.
Далее открывается транзистор Т2 и срабатывает реле включения инвертора. При нажатой кнопке S3 транзистор Т3 закрыт и на работу схемы не влияет.
Одновременно с этим подаётся напряжение на схему включения осциллятора.
Положительное напряжение с коллектора транзистора Т1 через стабилитрон ZD4 попадает на базу Т8 , открывшийся транзистор включает реле подачи напряжения на осциллятор. По истечении времени заряда конденсатора С5 транзистор Т7 закрывает транзистор Т8. Так время работы осциллятора ограничено 1-2 секундами. Что вполне достаточно для уверенного розжига дуги в плазмотроне.
Реализация временных задержек для осциллятора и воздушного клапана реализованы по сходным схемам.
При размыкании кнопки S3 снимается напряжение с обмотки реле REL 2 . Далее положительное напряжение через резистор R16 открывает транзистор Т3 который блокирует транзистор Т2 и реле управления инвертором обесточится. Одновременно с этим конденсатор С4 разряжается через резистор R23 и переход база эмиттер. Таким образом воздушный клапан выключается с необходимой задержкой. При повторном нажатии кнопки S3 процесс повторяется.
Детали.
Как оказалось самая большая проблема — это перекрыть поток воздуха. Для этих целей установлен клапан КИПиА времён СССР . Не смотря на надпись 1 атм. ДУ 2.5мм. Он с честью перекрывает 4 атм. Фильтр для очистки воздуха 1/4" Intrtool PT1412 выбран как самый доступный.
Трансформатор инвертора на кольце CF138-T6325-C первичная и вторичная обмотки намотаны в два провода диаметром 1.2 мм. Выходной дроссель на кольце из альсифера 46х25х18 проводом 1.5 мм до заполнения в один слой. Выбран именно этот дроссель т.к. в моём случае нет необходимости использовать токи более 20 А. Высоковольтный трансформатор намотан проводом 1.5мм из этих же соображений. Трансформатор осциллятора намотан на сердечнике ETD-39 проводом ПЭВ-2 -0.45 послойная и между обмотками изоляция обязательна.
Проверка инвертора.
На время проверки силовой части осциллятор и схема управления должны быть отключены. Разумеется контакты реле блокировки инвертора нужно замкнуть.
Перед включением необходимо проверить правильность монтажа. Первым проверяется источник питания , предусмотрена возможность его отдельного подключения через разъём JMP2. Затем необходимо убедится в наличии и правильности формы импульсов частотой 50 кГц. на затворах силовых транзисторов инвертора. Время "спада" не должно превышать 0,25us. Следующим шагом проверяется работа инвертора на эквивалент нагрузки. Я использовал два водяных ТЭНа по 5 кВт. соединённых параллельно. Максимальный ток устанавливается резистором R78. Минимальный ток при данной схеме не нуждается в регулировке. Его значение близко к 10 А. В конце статьи в файлах SDS00003 и SDS00004 приведены формы напряжения на коллекторе транзистора T8 инвертора при отсутствии тока и нагрузке 10 А.
Во время проверки ток в цепи нагрузки контролируется стрелочным амперметром с измерительным шунтом. Розжиг дуги и работа осциллятора проверяется импровизированным имитатором. Две медные проволоки диаметром 0.8 -1 мм. подключаются к аноду и катоду при этом обеспечивается зазор 2-3 мм. Электрическая дуга должна надёжно разжигаться с первого включения осциллятора. При этом медь естественно сгорает, а дуга тухнет.
Далее — пробный рез не толстого металла. Окрашенный желательно не использовать. Регулятором расположенном на фильтре установить давление воздуха 4 атм. Продуть резак воздухом 3-4 сек. для этого принудительно открыть воздушный клапан нажатием кнопки S2. Прикоснувшись соплом к заготовке нажать кнопку на ручке резака. При этом на 2 сек. включается осциллятор. И образовавшимся факелом плазмы резать, без особого нажима ведя по намеченной линии соплом.
Не стоит пренебрегать элементарными правилами ТБ. Величина выходного напряжения и тока могут быть опасны для жизни! Защита органов зрения обязательна!
Традиционно обсуждается на форуме все не написанное здесь.
Рекомендации по подбору параметров резки
Кислородная резка
Кислородная резка основана на сгорании металла в струе технически чистого кислорода. Металл при резке нагревают пламенем, которое образуется при сгорании какого-либо горючего газа в кислороде. Кислород, сжигающий нагретый металл, называют режущим. В процессе резки струю режущего кислорода подают к месту реза отдельно от кислорода, идущего на образование горючей смеси для подогрева металла. Процесс сгорания разрезаемого металла распространяется на всю толщину, образующиеся окислы выдуваются из места реза струёй режущего кислорода.
Металл, подвергаемый резке кислородом, должен удовлетворять следующим требованиям: температура воспламенения металла в кислороде должна быть ниже температуры его плавления; окислы металла должны иметь температуру плавления ниже, чем температура плавления самого металла, и обладать хорошей жидкотекучестью; металл не должен иметь высокой теплопроводности. Хорошо поддаются резке низкоуглеродистые стали.
Для кислородной резки пригодны горючие газы и пары горючих жидкостей, дающие температуру пламени при сгорании в смеси с кислородом не менее 1800 гр. Цельсия. Особенно важную роль при резке имеет чистота кислорода. Для резки необходимо применять кислород с чистотой 98,5-99,5 %. С понижением чистоты кислорода очень сильно снижается производительность резки и увеличивается расход кислорода. Так при снижении чистоты с 99,5 до 97,5 % (т.е. на 2 %) — производительность снижается на 31 %, а расход кислорода увеличивается на 68,1 %.
Технология кислородной резки. При разделительной резке поверхность разрезаемого металла должна быть очищена от ржавчины, окалины, масла и других загрязнений. Разделительную резку обычно начинают с края листа. Вначале металл разогревают подогревающим пламенем, а затем пускают режущую струю кислорода и равномерно передвигают резак по контуру реза. От поверхности металла резак должен находиться на таком расстоянии, чтобы металл нагревался восстановительной зоной пламени, отстоящей от ядра на 1,5-2 мм, т.е. наиболее высокотемпературной точкой пламени подогрева. Для резки тонких листов (толщиной не более 8-10 мм) применяют пакетную резку. При этом листы плотно укладывают один на другой и сжимают струбцинами, однако, значительные воздушные зазоры между листами в пакете ухудшают резку.
На машинах МТР "Кристалл" применяется резак "Эффект-М". Особенность резака — наличие штуцера для сжатого воздуха, который, пройдя через внутреннюю полость кожуха, истекает через кольцевой зазор над мундштуком и создает колоколообразную завесу, что локализует распространение продуктов сгорания и защищает элементы конструкции машины от перегрева.
Параметры режимов резки низкоуглеродистой стали приведены ниже в таблице 1:
Толщина | Сопло | Гильза | Камера | Давление | Скорость | Расход | Расход2 | Ширина | Расстояние |
мм | мПа | мм/мин | м.куб./час | м.куб./час | |||||
1 | 2 | 3 | 4 | 5 | 6 | 7 | 8 | 9 | 10 |
5 | 01 | 3П | 1ПБ | 0,3 | 650 | 2,5 | 0,5 | 3 | 4 |
10 | 2 | 0,4 | 550 | 3,75 | 0,52 | 3,3 | 5 | ||
20 | 0,45 | 475 | 5,25 | 0,55 | 3,5 | ||||
30 | 3 | 0,5 | 380 | 7 | 0,58 | 4 | 6 | ||
40 | 0,55 | 340 | 8 | 0,6 | 5 | ||||
50 | 0,6 | 320 | 9 | 0,65 | |||||
60 | 5П | 0,65 | 300 | 10 | 0,7 | ||||
80 | 4 | 0,7 | 275 | 12 | 0,75 | ||||
100 | 0,75 | 225 | 14 | 0,85 | 5,5 | 8 | |||
160 | 5 | 0,8 | 170 | 18 | 0,95 | 6 | 10 | ||
200 | 6 | 0,85 | 150 | 22 | 1,1 | 7,5 | 12 | ||
300 | 6П | 0,9 | 90 | 25 | 1,2 | 9 |
1. Толщина разрезаемого металла
5. Давление кислорода
6. Скорость резки
7. Расход кислорода
8. Расход пропана
9. Ширина реза
10. Расстояние до листа
Воздушно-плазменная резка
Процесс плазменной резки основан на использовании воздушно-плазменной дуги постоянного тока прямого действия (электрод-катод, разрезаемый металл — анод). Сущность процесса заключается в местном расплавлении и выдувании расплавленного металла с образованием полости реза при перемещении плазменного резака относительно разрезаемого металла.
Для возбуждения рабочей дуги (электрод — разрезаемый металл), с помощью осциллятора зажигается вспомогательная дуга между электродом и соплом — так называемая дежурная дуга, которая выдувается из сопла пусковым воздухом в виде факела длиной 20-40 мм. Ток дежурной дуги 25 или 40-60 А, в зависимости от источника плазменной дуги. При касании факела дежурной дуги металла возникает режущая дуга — рабочая, и включается повышенный расход воздуха; дежурная дуга при этом автоматически отключается.
Применение способа воздушно-плазменной резки, при котором в качестве плазмообразующего газа используется сжатый воздух, открывает широкие возможности при раскрое низкоуглеродистых и легированных сталей, а также цветных металлов и их сплавов
Преимущества воздушно-плазменной резки по сравнению с механизированной кислородной и плазменной резкой в инертных газах следующие: простота процесса резки; применение недорогого плазмообразующего газа — воздуха; высокая чистота реза (при обработке углеродистых и низколегированных сталей); пониженная степень деформации; более устойчивый процесс, чем резка в водородосодержащих смесях.
Рис. 1 Схема подключения плазмотрона к аппарату.
Рис. 2 Фазы образования рабочей дуги
а — зарождение дежурной дуги; б — выдувание дежурной дуги из сопла до касания с поверхностью разрезаемого листа;
в — появление рабочей (режущей) дуги и проникновение через рез металла.
Технология воздушно-плазменной резки. Для обеспечения нормального процесса необходим рациональный выбор параметров режима. Параметрами режима являются: диаметр сопла, сила тока, напряжение дуги, скорость резки, расстояние между торцом сопла и изделием и расход воздуха. Форма и размеры соплового канала обуславливают свойства и параметры дуги. С уменьшением диаметра и увеличением длины канала возрастают скорость потока плазмы, концентрация энергии в дуге, её напряжение и режущая способность. Срок службы сопла и катода зависят от интенсивности их охлаждения (водой или воздухом), рациональных энергетических, технологических параметров и величины расхода воздуха.
При воздушно-плазменной резке сталей диапазон разрезаемых толщин может быть разделён на два — до 50 мм и выше. В первом диапазоне, когда необходима надёжность процесса при небольших скоростях резки, рекомендуемый ток 200-250 А. Увеличение силы тока до 300 А и выше приводит к возрастанию скорости резки в 1,5-2 раза. Повышение силы тока до 400 А не даёт существенного прироста скоростей резки металла толщиной до 50 мм. При резке металла толщиной более 50 мм следует применять силу тока от 400 А и выше. С увеличением толщины разрезаемого металла скорость резки быстро падает. Максимальные скорости резки и сила тока для различных материалов и толщины, выполненные на 400 амперной установке приведены в таблице ниже.
Скорость воздушно-плазменной резки в зависимости от толщины металла: таблица 2
Разрезаемый материал | Сила тока А | Максимальная скорость резки (м/мм) металла в зависимости от его толщины, мм | ||||||
10 | 20 | 30 | 40 | 50 | 60 | 80 | ||
Сталь | 200 | 3,6 | 1,6 | 1 | 0,5 | 0,4 | 0,2 | 0,1 |
300 | 6 | 3 | 1,8 | 0,9 | 0,6 | 0,4 | 0,2 | |
400 | 7 | 3,2 | 2,1 | 1,2 | 0,8 | 0,7 | 0,4 | |
Медь | 200 | 1,2 | 0,5 | 0,3 | 0,1 | |||
300 | 3 | 1,5 | 0,7 | 0,5 | 0,3 | |||
400 | 4,6 | 2 | 1 | 0,7 | 0,4 | 0,2 | ||
Алюминий | 200 | 4,5 | 2 | 1,2 | 0,8 | 0,5 | ||
300 | 7,5 | 3,8 | 2,6 | 1,8 | 1,2 | 0,8 | 0,4 | |
400 | 10,5 | 5 | 3,2 | 2 | 1,4 | 1 | 0,6 |
Режимы. таблица 3
Разрезаемый материал | Толщина, мм | Диаметр сопла, мм | Сила тока, А | Расход воздуха, л/мин | Напряжение, В | Скорость резки, м/мин | Ширина реза (средняя), мм |
Низкоуглеродистая сталь | 1 — 3 | 0,8 | 30 | 10 | 130 | 3 — 5 | 1 — 1,5 |
3 — 5 | 1 | 50 | 12 | 110 | 2 — 3 | 1,6 — 1,8 | |
5 — 7 | 1,4 | 75 — 100 | 15 | 1,5 — 2 | 1,8 — 2 | ||
7 — 10 | 10 | 120 | 1 — 1,5 | 2 — 2,5 | |||
6 — 15 | 3 | 300 | 40 — 60 | 160 — 180 | 5 — 2,5 | 3 — 3,5 | |
15 — 25 | 2,5 — 1,5 | 3,5 — 4 | |||||
25 — 40 | 1,5 — 0,8 | 4 — 4,5 | |||||
40 — 60 | 0,8 — 0,3 | 4,5 — 5,5 | |||||
Сталь 12Х18Н10Т | 5 — 15 | 250 — 300 | 140 — 160 | 5,5 — 2,6 | 3 | ||
10 — 30 | 160 — 180 | 2,2 — 1 | 4 | ||||
31 — 50 | 170 — 190 | 1 — 0,3 | 5 | ||||
Медь | 10 | 300 | 160 — 180 | 3 | |||
20 | 1,5 | 3,5 | |||||
30 | 0,7 | 4 | |||||
40 | 0,5 | 4,5 | |||||
50 | 0,3 | 5,5 | |||||
60 | 3,5 | 400 | 0,4 | 6,5 | |||
Алюминий | 5 — 15 | 2 | 120 — 200 | 70 | 170 — 180 | 2 — 1 | 3 |
30 — 50 | 3 | 280 — 300 | 40 — 50 | 170 — 190 | 1,2 — 0,6 | 7 |
Режимы воздушно-плазменной резки металлов. таблица 4
Разрезаемый материал | Толщина, мм | Диаметр сопла, мм | Сила тока, А | Скорость резки, м/мин | Ширина реза (средняя), мм |
Сталь | 1 — 5 | 1,1 | 25 — 40 | 1,5 — 4 | 1,5 — 2,5 |
3 — 10 | 1,3 | 50 — 60 | 1,5 — 3 | 1,8 — 3 | |
7 — 12 | 1,6 | 70 — 80 | 1,5 — 2 | 1,8 — 2 | |
8 — 25 | 1,8 | 85 — 100 | 1 — 1,5 | 2 — 2,5 | |
12 — 40 | 2 | 110 — 125 | 5 — 2,5 | 3 — 3,5 | |
Алюминий | 5 — 15 | 1,3 | 60 | 2 -1 | 3 |
30 — 50 | 1,8 | 100 | 1,2 — 0,6 | 7 |
Рис. 3 Области оптимальных режимов резки металлов для плазмотрона с воздушным охлаждением (ток 40А и 60А)
Рис. 4 Области оптимальных режимов для плазмотрона с воздушным охлаждением (ток 90А).
Рис. 5 Зависимость выбора диаметра сопла от тока плазмы.
Рис. 6 Рекомендуемые токи для пробивки отверстия.
Скорость воздушно-плазменной резки, по сравнению с газокислородной, возрастает в 2-3 раза (см. Рис. 7).
Рис. 7 Скорость резки углеродистой стали в зависимости от толщины металла и мощности дуги.
Пологая нижняя линия — газокислородная резка.
При воздушно-плазменной резке меди рекомендуется применять силу тока 400 А и выше. Замечено, что при резке меди с использованием воздуха во всём диапазоне толщины и токов образуется легко удаляемый грат.
Хорошего качества реза при резке алюминия, с использованием воздуха в качестве плазмообразующего газа, удаётся достигнуть лишь для небольших толщин (до 30 мм) на токах 200 А. Удаление грата с листов большой толщины затруднительно. Воздушно-плазменная резка алюминия может быть рекомендована лишь как разделительная при заготовке деталей, требующих последующей механической обработки. Припуск на обработку допускается не менее 3 мм.
#1 As из sd
поджиг дуги плазмореза Плазма. Резка металла
Просто хочу внести ясность
На форуме. На сайтах покупок. В паспортах аппаратов. Везде вкралась ложь
Все делят поджиг на две категории. Контактный и бесконтактный
Оказывается контактный тоже бесконтактный( сам пробовал)
Бесконтактный это
1 поджиг с дежурной дугой
2 контактный это поджиг HF высокочастотный поджиг ( тоже бесконтактный пожиг) просто неточности перевода
В плазморезах не может быть КОНТАКТНОГО поджига
Катод скрыт внутри горел
Бывает только поджиг с дежурной дугой и прямой поджиг
Прямой поджиг это высокочастотный поджиг сразу между катодом и металлом
#2 Миротворец

- Город: г. Иркутск. Александр, можно на ты
В плазморезах не может быть КОНТАКТНОГО поджига
Вы не правы, есть плазморезы с контактным поджигом дуги(обычно с дежурной дугой), с высокочастотным поджигом и с поджигом касанием. У контактного поджига анод и катод постоянно замкнуты и при включении резака происходит размыкание цепи(внутренний электрод подпружиненный) с зажиганием дежурной дуги. Это и есть контактный поджиг
#3 As из sd
#4 As из sd
У контактного поджига анод и катод постоянно замкнуты и при включении резака происходит размыкание цепи(внутренний электрод подпружиненный) с зажиганием дежурной дуги. Это и есть контактный поджиг
ЦЕПЬ ЭТО АППАРАТ И ДЕТАЛЬ
цепь катод-сопло это внутри аппаратная цепь и контактом между аппаратом и деталью быть не может
Это НИЗКОВОЛЬТНЫЙ БЕСКОНТАКТНЫЙ ПОДЖИГ
#5 Илария
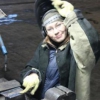
- Город: Саратов
As из sd, не стоит так часто использовать Капслок (только заглавные буквы), Вас итак прочтут и поймут. Да и точки в конце предложения (каждого) весьма приветствуются. Особенно — мной. Устное предупреждение за оформление постов.
#6 Рабиндранат Кагор
Судя по названию темы, ТС собрался облить бензином плазморез и поднести спичку.
#7 copich
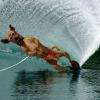
- Город: Москва
Рассусоливать эту тему нет ни желания ни времени. Т.е. спорить не буду. А вот Миротворца я поддерживаю.
Делить, вычетать, складывать и умножать не будут. Мнение мое:
два поджога. Контактный поджог, это когда анод и катод замкнуты в свободном положении. Когда нажимаете кнопку старта, то подается воздух под давлением и размыкает ЦЕПЬ между анодом и катодом. При размыкании образуется дуга. Вы видели как проскакивает дуга когда выключатель света дома выключаете?! Вот тут тот же эффект. Когда зажигается дежурная дуга образуется цепь между электродом и деталью за счет именно этой дуги вы начинаете резать. Если аппарат не увидел цепи, то дуга прерывается (краска, ржавчина и т.п.).
Безконтактный — осциллятор пробивает зазор между анодом и катодом, далее все как обычно — дуга организует цепь между электродом и деталью.
Начните себя уважать и тогда вас то же будут уважать.
работайте на оборудование которое будет доставлять вам радость и тогда работа будет в сладость!
#8 Миротворец

- Город: г. Иркутск. Александр, можно на ты
Вы опять не правы, потому что на этих горелках есть своя масса, то есть своя цепь и для горения дуги не нужна деталь.
Если аппарат не увидел цепи, то дуга прерывается (краска, ржавчина и т.п.).
Если кнопка нажата, то дуга не тухнет за счёт дежурной дуги, если она присутствует на данной модели аппарата.
#9 copich
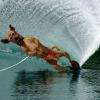
- Город: Москва
Если кнопка нажата, то дуга не тухнет за счёт дежурной дуги, если она присутствует на данной модели аппарата.
Если основной дуги нет (т.е. аппарат не перешел в режим реза), то вспомогательная дуга горит не долгое время. несколько сек. Повторное нажатие, повторно зажигает дежурную дугу и есть возможность начать резать.
Начните себя уважать и тогда вас то же будут уважать.
работайте на оборудование которое будет доставлять вам радость и тогда работа будет в сладость!
#10 Миротворец

- Город: г. Иркутск. Александр, можно на ты
copich,Да, так и есть. Такие резаки отлично справляются с грязью, краской, ржавчиной т.п., что не скажешь про ВЧ поджиг, а про поджиг касанием вообще молчу(был у меня такой, чуть ржа и хоть плачь))).
#11 copich
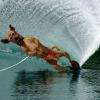
- Город: Москва
copich,Да, так и есть. Такие резаки отлично справляются с грязью, краской, ржавчиной т.п., что не скажешь про ВЧ поджиг, а про поджиг касанием вообще молчу(был у меня такой, чуть ржа и хоть плачь))).
Может уже глубоко копаю и не потеме. Но все же, спрошу. А почему ВЧ поджог по вашим словам является причиной затрудненного реза? Какая разница, плазмотрон на весу или касательно по металлу перемещается? Если дежурная пробила краску и грязь, то дуга основная полюбасу поджигается. А если источник перешел на основную дугу, то реж без остановки скоко душе угодно. Главное отличие это удобство реза и какие толщины вы будуте резать.
А касательный поджог дуги о металл — это не промышленное оборудование либо технологии прошлых лет. О чем я не хочу и говорить. Ведь когда говорят о огороде, не говорят о палке-копалке. А почему не промышленное оборудование, так потому что китайцы применяют технологии 80-х годов и толкают на наш рынок эту дешевку. Если что-то современное, то уже нет касательного поджога о металл.
Начните себя уважать и тогда вас то же будут уважать.
работайте на оборудование которое будет доставлять вам радость и тогда работа будет в сладость!
#12 Миротворец

- Город: г. Иркутск. Александр, можно на ты
А почему ВЧ поджог по вашим словам является причиной затрудненного реза?
Какая разница, плазмотрон на весу или касательно по металлу перемещается?
На весу резать сложнее, мои горелки не боятся соприкосновения. Если в аппарате есть дежурная дуга, то с резкой вообще нет никаких проблем.
А касательный поджог дуги о металл — это не промышленное оборудование либо технологии прошлых лет.
Отправить ответ