Плазменный резак на воде
Содержание:
Здравствуйте, нужна помощь профессионалов!
Ситуация следующая – собираю стол плазменного раскроя металла, работа медленно, но все же продвигается.
Подобрал аппарат воздушно-плазменной резки: http://www.voltup.ru/svarochnoye-oborudovaniye/aurora-airforce-60-igbt-cut-60g.html Но наткнулся в своих поисках на аппарат многофункциональный универсальный инструмент для плазменной резки и сварки металла http://www.rk-snab.ru/audit/apparaty-plazmennoj-rezki/plazmennyj-kompleks-dlja-rezki-i/
Теперь о задачах которые должен решать мой доморощенный станок – толщина обрабатываемого металла – до 2 мм. Скорость резки – не решающий фактор.
Попытаюсь изложить тезисно свои соображения и сомнения по поводу этих методов резки, потому что слишком много пробелов:
А – воздушно-плазменная резка
+ Все кто занимается плазменным раскроем используют именно этот метод
+ Может резать до 15 мм (хотя мне хватит и 2 мм)
– Шумно из-за 5 атм подведенных к плазморезу
– 100% будет терять дугу при проезде над уже имеющимися прорезами и отверстиями (из-за бюджетности источника нет дежурной дуги), но знающие люди говорят что это лечится правильным перезапуском. Кстати еще источник необходимо дооборудовать контроллером высоты факела http://purelogic.ru/shop/stanki_cpu/aksessuary_dlya_ plazmennoj_i_gazovoj_rezki/kontrol_vysoty_fakela_rezaka_thc/ kontroller_thc1_interfejs_ethernet_up_down/
– . Высокочастотный поджиг с его вечными помехами.
– В сумме набегает приличная сумма
Б – "паро"-плазменная резка.
– Не понятен реальный коэффициент полезного времени, точнее чем он ограничен, ведь если зарядом воды в резаке, то поскольку резка механизированная, то его можно дооборудовать чем то вроде капельницы. Если перегревом блока управления, то по той же причине можно улучшить охлаждение
– Мало информации и малое распространение
– До конца не понятен механизм контроля высоты факела
– Скорее всего хуже качество врезки при вырезании отверстий
Теперь из плюсов касающихся лично меня
+ Меньшее энергопотребление
+ Намного тише
+ Судя по фото и видео качество реза 1,5 мм стали вполне приемлемое
+ Факел разжигается перед началом резки и поддерживается на всем протяжении резки (экономия расходников и никакого высокочастотного поджига. )
В общем какая то каша в голове, помогите навести порядок.
- 8646 просмотров
Вот были аппараты водоплазменной резки:
В советской литературе было упоминание о появлении варианта плазменной резки с добавлением небольшого количества воды в плазму, в азотную или воздушную.
Но этот вариант был направлен скорее не на замену плазмообразующего газа водяным паром, а на улучшение качества реза, так как часть воды превращалось в пар, что увеличивало давление струи, а часть так и шла в струе, тем самым дополнительно защищая место резки (сварки) и охлаждало его.
Был даже разработан плазмотрон ПМР-74 (см. рис.), который отличался наличием дополнительного канала для подачи воды, расход которой составлял – 0,004-0,006 л/с.
Современные паровые плазмотроны, как я понимаю, являются развитием конструкции плазмотрона ПМР-74, только в современном случае речь идет не о добавлении воды в плазмообразующий газ, а о использовании вместо него паров воды (в некоторых случаях – органического растворителя).
Учитывая, что при испарении 1 см 3 воды образуется около 1700 см 3 вполне можно использовать небольшое количество воды для плазменной резки. Т.е. когда в плазмотроне зажигается электрическая дуга, она превращает в пар, а после в плазму содержащуюся там воду. В момент, когда пар ионизируется, естественное давление выталкивает его из сопла.
В продаже нашел основные три варианта:
– Мультиплаз-3500 (рис.1)
– PLAZARIUM SP3 (бывший Плазар) (рис.2)
– Горынычъ (рис.3)
У каждого, как я понимаю, есть свои особенности.
Здесь на видеоролике можно посмотреть как производят резку на аппарате Мультиплаз-3500 в режиме 1.
Здесь на видеоролике можно посмотреть как производят резку на аппарате Мультиплаз-3500 в режиме 2.
Обратите внимание, что при использовании режима 2, заземляют само изделие, что говорит о том, что резка будет проводиться дугой прямого действия, а не косвенного, как в режиме 1. Т.е. плазмотрон универсален.
Здесь на видеоролике можно посмотреть подробное описание аппарата Горынычъ, а главное – увидеть во всех деталях устройство плазмотрона.
А также можно обратить внимание, что для получения более мощной плазмы, подключают уже компрессор, т.к., как я понимаю (и как видно из демонстрации процесса резки без компрессора), струя плазмы, образованной давлением пара, весьма слабенькая.
Нашел Решение патентного спора АСиПП (Горынычъ) с компанией «Мультиплаз».
Кстати, полагаю, что в следствие патентов, а также невысокой мощности плазмы и необходимости добавления воды, способ не получил большого распространения.
Реклама в сети гласит, что процесс получается "дешевым и сердитым". А комментарии наоборот:
Перед включением в горелку заливается вода или спирт. В течение минуты после заправки и зажигания дуги аппарат прогревается, поплевываясь каплями жидкости.
В режиме резки аппарат работает красиво – из сопла вырывается длинная тонкая раскаленная струя, похожая на иглу, в воздухе пахнет электричеством.
А вот эффективность низкая. Струя конечно злая, почти сразу начинает окислять железо и выдувать его в виде расплава окисла…но очень локально. Явно видно, что аппарат маломощный. Из-за этой самой маломощности злое действие плазменной струи очень-очень локальное и скорость процесса резки в результате низкая.
Трёхмиллиметровую мягкую сталь опробованный аппарат резал со скоростью примерно 1 ммсек. 12 мм пруток разрезать все-таки удалось в несколько приемов, но время процесса исчислялось минутами (болгаркой наверное раз в 20 быстрее).
Имхо рационально использование аппарата для фигурной резки металла толщиной в 0,5-1,5 мм. В случае такой толщины скорость будет больше, а небольшая ширина реза (менее миллиметра) и локальность злого действия плазмы дадут неплохую точность.
Резюме – аппарат маломощный и недоведёный. Брать не буду. Имеющиеся инвертор и болгарка возможностей дают много больше, а стоят (вместе!) на треть меньше.
Мультиплаз-3500 По сравнению с вышеописанным «Плазаром» сразу видна МОЩЬ. Аппарат быстро прогревает показанные на снимке трубу с 4 мм стенкой и пластинку с 5 мм.
Заявляемая производителями цена 50 тысяч рублей чрезмерна, ибо аппарат имеет крупные недостатки-недоработки, а «конкуренты» — газовые горелки, инверторы, инверторные полуавтоматы вдвое-впятеро-десятеро дешевле и имеют значительно меньше недостатков.
Импортные плазморезы вдвое дешевле, при том что мощнее.
Первый и наибольший недостаток – довольно быстро (5-7 минут) заканчивается рабочая жидкость. Приходится останавливать сварку и заправлять горелку вновь. За это время шов остывает, горелку тоже раскочегаривать заново – потери времени.
Далее – «пистолет» не удобен для сварки в сложных положениях. Горелка должна иметь форму классической газовой горелки с отогнутым соплом. Газовое питание позволит избыть большой резервуар-пистолет и довести эргономичность до нормальной.
Резюме – идея плазменной сварки/резки перспективная, отечественные производители сыроделы и лодыри.
Патент №2103129 Способ плазменно-дуговой сварки металлов
(Мультиплаз-3500)
Способ плазменно-дуговой сварки металлов может быть использован в машиностроении, строительстве и других отраслях промышленности. Плазменно-дуговую сварку металлов выполняют сжатой дугой прямого или косвенного действия. В качестве плазмообразующей среды используют пары жидкости, содержащей воду с добавлением органического растворителя в виде кислородсодержащих соединений углеводородов. В качестве органического растворителя может быть применен спирт. Парообразование осуществляют непосредственно в плазменной горелке.
Известны способы плазменно-дуговой сварки металлов сжатой дугой косвенного действия, в которых плавление металла производится плазменной струей [1, 2]. Известны способы сварки металлов сжатой дугой прямого действия, возбуждаемой между электродами плазмотрона и обрабатываемым изделием [3, 4].
Упомянутые способы предусматривают образование плазменной струи путем обжатия дугового разряда инертным газом. Они позволяют получить качественные сварные соединения, однако наличие внешнего источника инертного газа создает эксплуатационные неудобства, а высокая стоимость производства инертного газа и значительные расходы по заправке баллонов существенно ограничивают возможности использования. К тому же при обработке легкоокисляющихся металлов необходимо помимо плазмообразующего газа подавать в плазмотрон и защитный [5].
Известны плазменные горелки (плазмотроны), в которых для создания плазменной струи используют водяной пар, подводимый от специального парогенератора или вырабатываемый непосредственно в горелке путем испарения жидкости за счет тепла, выделяемого электродами [6]. Последняя из упомянутых плазменных горелок наиболее экономична и проста в эксплуатации, однако использование ее для сварки затруднено из-за интенсивного окисления металла, вызываемого присутствием в плазменной струе паров воды, а также молекул и атомов кислорода.
Сущность изобретения заключается в том, что в способе плазменно-дуговой сварки металлов сжатой дугой прямого или косвенного действия, включающем обжатие дуги плазмообразующей средой с получением плазменной струи, в качестве плазмообразующей среды используют пары жидкости, содержащей воду с добавлением органического растворителя в виде кислородсодержащих соединений углеводородов, обладающих способностью предотвращать вступление атомов и молекул кислорода, содержащихся в парах, в окислительную реакцию с обрабатываемым металлом.
Экспериментально показано, что наилучший результат дает использование в качестве добавок к воде спиртов, а оптимальным с точки зрения энергетики и прочности сварного шва является содержание их в парообразующей жидкости в пределах 30-50%. При уменьшении содержания спиртов в смеси ниже нижнего предела увеличивается присутствие окалины в сварном соединении, что в свою очередь снижает его прочностные характеристики. При превышении содержания спиртов в смеси 50% понижается смешиваемость органического растворителя с водой, что приводит к расслоению смеси и неравномерному ее испарению. К тому же при этом падает энтальпия пара, что с свою очередь понижает температуру плазменной струи. Наилучший результат дало использование для сварки плазменной горелки, в которой плазмообразующий пар получен из наиболее распространенной в быту жидкости, содержащей 60% воды и 40% этилового спирта.
Парообразование может быть произведено непосредственно в плазменной горелке путем испарения жидкости, заполняющей специальный резервуар, за счет тепловой энергии, выделяемой горящей дугой на электродах горелки.
Осуществление заявленного способа плазменно-дуговой сварки возможно посредством плазмотронов как косвенного действия, при котором тепловая энергия передается обрабатываемому изделию непосредственно плазменной струей, выходящей из сопла-анода горелки, так и посредством плазмотронов прямого действия, в которых воздействие на изделие производится дугой, стабилизированной плазменной струей. Во втором случае для плавления металла используется не только энергия плазменной струи, но и энергия электрической дуги, что существенно улучшает энергетические характеристики способа.
На фиг. 1 схематично изображено устройство, осуществляющее сварку металлов дугой косвенного действия. Оно состоит из плазменной горелки (плазмотрона), включающей катод 1, сопло-анод 2 с каналами для плазмообразующей среды, заполненный влаговпитывающим материалом резервуар 3 с патрубком 4, электроизоляционную крышку 5, а также источник питания 6 с регулятором тока 7. В качестве влаговпитывающего материала могут быть использованы каолиновая вата, стекловата, стеклоткань, углеткань, углевойлок, а в качестве парообразующей жидкости, например, смесь воды со спиртом или ацетоном.
Плазменные аппараты сварки, резки, пайки приобрели обширное распространение за счет обеспечения возможности выполнения задач с высокой эффективностью в короткие сроки. При помощи них можно работать практически с любым металлом и электропроводящими материалами.
Аппарат для плазменной резки и сварки: описание
Резка происходит путем плавления и смешения металла с высокотемпературной плазмой, которая создается электрической дугой из инертного вещества. Так, в устройстве атмосферный ионизированный воздух направляется через отверстие в горелке под давлением в необходимом количестве и переводится в состояние плазмы.
Итоговый результат и эффективность могут быть улучшены при использовании нескольких видов инертного газа, что особенно актуально для цветных металлов. Именно поэтому стоит проявить внимательность при подборе устройств и учесть все параметры.
Выбор
Аппарат для плазменной резки и сварки подходит для обработки тугоплавких, цветных металлов (алюминия, меди), черного метала (чугун, нержавеющая сталь и варианты с различным легированием), а также других типов материалов. Сегодня в магазинах представлен обширный ассортимент инструментов, для выбора оптимального варианта необходимо определиться с имеющимися задачами и условиями эксплуатации. После этого производится выбор из подходящих моделей.
Главным критерием являются материалы, с которыми может работать устройство. Рекомендуется выбирать агрегат с широким набором функций и возможностью резки различных металлов. При этом нужно отметить, что стоимость напрямую зависит от функционала и известности марки. Также нужно обратить внимание на размеры толщины резки. Чаще всего данный параметр указывается для листов из стали, реже всего можно встретить обозначение для нержавейки. По этой информации можно понять возможности резки различных вариантов.
Поджиг дуги
Все модели объединены идентичной схемой работы и общим конструктивным исполнением, при этом данные параметры одинаковы у любых изготовителей. Различие заключается в способе поджига дуги, здесь возможны следующие варианты:
- Включение пилотной дуги возбуждает плоскость основного элемента. То есть вначале приводится в действие пилотная дуга с низкой мощностью, которая находится на дополнительном контуре плазмотрона. При помощи сжатого воздуха образуется дуга, она замыкается на плоскости материала, тем самым формируя главную дугу. Аппарат для плазменной резки и сварки с подобным методом поджига является оптимальным вариантом для работ с металлической обрешеткой и сеткой.
- Возбуждение с высокой частотностью. В этом случае формирование дуги происходит только при условии электрического разряда между головкой плазмотрона и листом материала. Такая методика сегодня является наиболее распространенной.
- Контактный поджиг. Дуга возникает при соприкосновении с заготовкой. Чаще всего можно встретить на приспособлениях бюджетной категории, отличающихся небольшой силой тока. Они характеризуются быстрым износом сопла плазматрона и других его деталей. В настоящее время изготовители все чаще устанавливают другие варианты поджига.
Принимая в расчет информацию, указанную выше, будет проще определиться с желаемой моделью и не ошибиться с имеющимися свойствами.
Преимущества и недостатки
Аппарат для плазменной резки и сварки, фото которого представлено выше, обладает множеством положительных сторон, среди которых стоит отметить следующие:
- Качество резки характеризуется высокой точностью и аккуратностью. Даже при наличии небольшого опыта соответствующих работ легко предотвратить такие недочеты, как наплывы и грат на обрабатываемых поверхностях.
- Безопасность. Вероятность возгорания сводится к минимуму при отсутствии взрывоопасных и воспламеняемых газов. Аналогичные характеристики способен обеспечить лишь дуговой ручной метод.
- Отсутствие деформации листов, волн и трещин на металлических поверхностях.
Некоторые устройства отличаются достаточно высокой стоимостью, что является единственным недостатком. При этом всегда можно постараться подобрать вариант с подходящей ценой и необходимыми характеристиками. Для осуществления резки в домашних условиях будет вполне достаточно агрегата со средними мощностными характеристиками.
“Горынычъ”
Устройство “Горынычъ” — аппарат плазменной сварки и резки российского производства подходит для работ, связанных с высокотемпературным воздействием. Возможно использование как для металлов, так и для других категорий материалов, не подверженных горению. Он представляет собой электродуговой генератор плазмы, образуемой при нагреве электронной дуги. Испарения рабочего состава, доходя до температуры ионизации, выводятся плазменной струей под давлением. В качестве рабочей жидкости может выступать этиловый спирт или вода, выбор того или иного варианта осуществляется в соответствии с поставленными задачами. Струя при этом имеет температуру в пределах 6000 градусов. Главными элементами аппарата являются блок управления и плазменный генератор.
“Горынычъ”, аппарат плазменной сварки и резки, отзывы в основном получает положительные. Многие пользователи отмечают его высокую скорость работы и многофункциональность.
“Сварог CUT 40 B”
Устройство отличается небольшим весом и компактными габаритами, его главное предназначение заключается в обработке тонких материалов. Оно создано на основе инверторной схемы и специальных транзисторов. Агрегат оснащается евроразъемом для горелки и удобной панелью управления. В процессе работ не возникает деформация материала, при этом желательно резать листы с толщиной в пределах 0,12 см.
Он имеет следующий принцип работы: ток подходит к электроду плазмотрона, сам плазменный факел поджигается осциллятором с высокой частотностью после нажатия на кнопку.
- отсутствие возможности опрокидывания благодаря достаточной устойчивости;
- экономичность;
- низкая стоимость;
- нет необходимости в создании определенных условий работ;
- интуитивно понятное управление;
- удобная перевозка за счет специальной рукояти и небольшой массы.
Среди недостатков стоит отметить невысокий ресурс плазматронного устройства.
Rilon CUT 40
Данный агрегат, так же, как и аппарат плазменной сварки, резки металла “Горынычъ”, позволяет работать с любыми типами токопроводящих основ: это различные сплавы, оцинкованная сталь, алюминий, медь. Бесконтактный поджиг работает на высокочастотном управлении. Возможно использование для материалов с толщиной около 20 мм, благодаря высокому уровню режущего тока. Степень воздействия зависит от толщины заготовки и характеристик металла. При помощи цифрового индикатора устанавливаются необходимые критерии.
- используется в широком диапазоне температур;
- обеспечивает обработку любых сплавов и материалов;
- основан на современной технологии;
- отличается высокой скоростью резки и качественным формированием шва;
- не возникает деформация заготовки.
Стоит отметить, что устройство не подходит для промышленных условий и активного использования.
BRIMA CUT-120
Аппарат для плазменной резки и сварки отличается небольшой массой основного трансформатора и компактными размерами, при этом он оптимально подходит для использования при демонтаже металлических конструкций. Применяется для работ с медью, цветным металлом, углеродистой и нержавеющей сталью с толщиной не более 35 мм. Состоит из газового редуктора, обратного силового провода и воздушного рукава.
- экономичность;
- постепенное изменение основных параметров процесса;
- качественное отведение тепла благодаря наличию множества отверстий в корпусе;
- возможность регулировки дуги;
- эффективная резка материала;
- легкая и чистая обработка металлических элементов с большой толщиной;
- высокая скорость проведения работ.
FUBAG PLASMA 40
Аппарат для плазменной резки и сварки подходит для любых токопроводящих материалов с толщиной не более 12 мм. Расходные элементы, такие как катод и сопло, отличаются длительным периодом использования. Поджиг дуги имеет высокочастотное управление.
- обеспечивает быструю резку заготовок;
- возможно подключение к стандартной сети 220 В, благодаря чему расширяется область использования и упрощается эксплуатация;
- достаточно надежный резак;
- образуется качественный шов без наплывов.
Способы плазменной резки постоянно улучшаются. Основная цель, которая ставится при проработке усовершенствований, состоит в уменьшении загрязнения окружающей среды, повышении производительности резки и в улучшении качества кромки реза. Конечной целью является создание двух плоскопараллельных ровно обрезанных поверхностей, которые перед передачей их на следующий этап технологической цепочки требуют минимальной окончательной обработки, либо вовсе в ней не нуждаются.
В зависимости от того, какой материал требуется разрезать, какова толщина этого материала, а также исходя из характеристик, обеспечиваемых источником питания, делается выбор из многочисленных вариантов выполнения плазменной резки.
Эти варианты, главным образом, различаются по конструкции применяемого плазменного резака, по системе подачи материала и по материалу, из которого выполнен электрод. На рис. 8 даётся общее представление различных опций, которые могут быть предусмотрены в конструкции плазменного резака.
Рисунок 8: Исполнения плазменных резаков |
![]() |
DIN 2310-6 устанавливает различия между следующими типами плазменных резаков, исходя из типа конструкции.
• Традиционная плазменная резка/ стандартная плазменная резка
• Плазменная резка с вторичной средой
• Плазменная резка с вторичным газом
• Плазменная резка с вторичной водой
• Плазменная резка с впрыскиванием воды
• Плазменная резка с повышенным обжатием
3.1 Традиционная резка
В стандартных машинах плазменной резки резак относительно прост, его конструкцией предусматривается использование только одного вида газа – режущего газа. В качестве режущих газов обычно применяют азот, кислород или смесь аргона с водородом (рис. 9).
Плазменная дуга обжимается только по внутреннему диаметру сопла, поверхности реза, характерные для этого метода имеют скос. Обычно плазменный газ проходит вокруг электрода, касаясь его. В зависимости от скорости резки охлаждение резака производится либо воздухом, либо водой. Поставляемые системы традиционной плазменной резки способны резать металл толщиной до 160 мм.
Рисунок 9: Традиционная (сухая) резка |
3.2 С вторичной средой
Вторичная среда создаётся вокруг плазменной дуги, для того чтобы вокруг неё была особая атмосфера. В качестве вторичной среды может использоваться либо вода, либо определённый вид газа (рис. 10).
Плазменная резка с водяным экраном
Плазменная резка с использованием воды в качестве вторичного экрана – это ещё один вариант плазменной резки с вторичной средой. Водяной экран выпускается струёй, разрываемой плазменной дугой. Благодаря восстановительному действию водорода, выделяющегося в ходе данного процесса, получаемая поверхность приобретает металлический блеск. Таким образом, плазменная резка с использованием водяного экрана является предпочтительным методом при работе с алюминием и высоколегированными сталями толщиной до 50 мм (рис. 10).
Рисунок 10: Резка со вторичной струей |
![]() |
Резка с вторичным газом
Подача вторичного газа вокруг плазменной дуги позволяет добиться ещё большего её обжатия и создания вокруг неё особой атмосферы. Благодаря этому повышается плотность энергии, качество реза и скорость резки. Если установить экранирующий колпачок определённым образом, то можно исключить возможность повреждения системы коротким замыканием и двойной дугой и, тем самым продлить срок службы расходных деталей. Обычно такую защитную среду называют также «вторичный газ», «экранирующий газ», «защитный газ» или «газ, образующий завихрения». Поставляемые машины, в которых применяется данный способ, в настоящее время способны резать листовой металл толщиной до 75 мм (рис. 11).
Рисунок 11: Сухая резка со вторичным газом |
![]() |
3.3 С впрыскиванием воды
При этом методе плазменная дуга подвергается дальнейшему обжатию за счёт впрыскивания воды, производящегося в радиальном направлении вокруг этой дуги. Испаряется только незначительная часть воды. Остальное количество воды охлаждает сопло и изделие. Охлаждение изделия впрыскивающейся водой, а также высокая скорость резки обеспечивает отсутствие поводок при резке, малое количество грата и, кроме того, продлевает срок службы расходных деталей. Методы резки с впрыскиванием воды подразделяются на два типа, различающихся по способу впрыскивания воды: радиальное впрыскивание и вихревое впрыскивание. При вихревом впрыскивании одна кромка реза получается почти вертикальной, тогда как другая скошена приблизительно на 5 – 8 градусов (рис. 12).
Рисунок 12: Плазменная резка с впрыскиванием воды |
![]() |
При использовании резака с впрыскиванием воды важно производить резку изделия таким образом, чтобы сторона со скошенной кромкой находилась там, где материал имеет заострённую форму, для такого метода лучше подходят плоские электроды. Данный метод применим исключительно к машинам подводной резки. Таким способом можно резать листовой металл толщиной от 3 до 75 мм.
3.4 Плазменная резка с повышенным обжатием
В данном варианте применяется повышенная плотность дуги, достигающаяся за счёт использования сопл с большим обжатием. Различные компании используют разные способы (некоторые из которых запатентованы) для обжатия дуги. Движение газа по кругу (рис. 13) и регулируемые сопла (рис. 14) в общем зарекомендовали себя как эффективные. Плазменная дуга, создаваемая с помощью такой системы позволяет выполнять вертикальный рез с большой точностью на листах металла толщиной от 0,5 до 25 мм. Плазменная резка с повышенным обжатием является предпочтительным методом, в случаях, когда используется вторичный газ.
Рисунок 13: Резка с повышенным обжатием |
![]() |
Рисунок 14: С повышенным (регулируемым) обжатием |
![]() |
В дополнение к описанным выше основным методам в литературе можно найти описание множества способов, являющихся собственностью компаний, при чём некоторые из них запатентованы.
В табл. 2 представлены обозначения основных вариантов, принятые в компании.
Таблица 2: Классификация обозначений основных вариантов резки, принятых в компании
Основные варианты плазменной резки
Традиционная
С вторичным газом
С водяным экраном
С впрыскиванием воды
С повышенным обжатием
Метод Dual flow (двойной поток)
X
Плазменный метод FineFocus (тонкая фокусировка)
X
Плазменный метод HiFocus (высокая фокусировка)
X
X
Плазменный метод High (высокий)
Х
Х
High current (большая сила тока)
X
X
Плазменный метод Hy Definition (высокая чоткость)
X
X
Плазменный метод LongLife (длительный срок службы)
X
X
X
Precision (с высокой точностью)
Х
Х
Water vortex (завихрение воды)
Х
Плазменный метод WIPC
X
Плазменный метод Swirling-gas (газ завихрения)
Х
X
Метод XLLife-Time (очень длительный срок службы)
X
X
X
(Источник: информационный листок DVS 2107)
3.5 Другие варианты резки
Данный вариант обеспечивает значительное повышение безопасности в работе. Резка осуществляется на глубине приблиз. от 60 до 100 мм под поверхностью воды (рис. 15) со значительным уменьшением шума, количества пыли и аэрозольного загрязнения окружающей среды. Уровень шума находится намного ниже величины 85 дБ (А). Вода также снижает величину ультрафиолетового излучения, имеющего место в процессе резки. Разрезанные детали имеют маленькие поводки.
Рисунок 15: Резка под водой |
![]() |
Поскольку подводная резка требует больше энергии, чем необходимо для резки в атмосферных условиях, скорости при плазменной резке под водой ниже.
Конструкционные стали толщиной приблизительно 15 мм, а также высоколегированные стали, имеющие толщину около 20 мм обычно экономически выгоднее резать под водой.
Плазменная строжка (рис. 16) – это процесс снятия материала с поверхности изделия с помощью плазменной дуги. Тепло, подводимое плазменной дугой, позволяет удерживать материал в расплавленном состоянии. Давление плазменной дуги помогает вытеснять расплавленный металл из зоны резки.
Рисунок 16: Плазменная строжка, выполняемая вручную
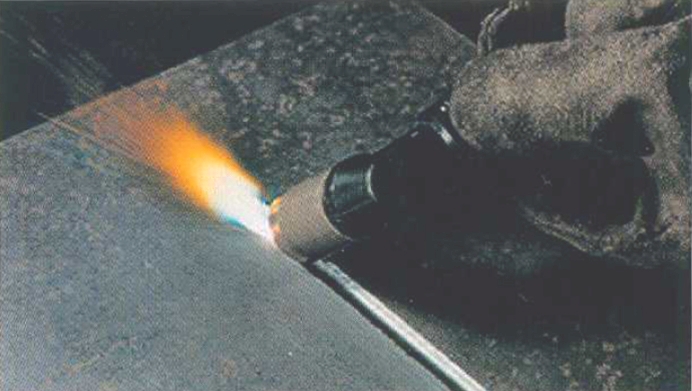
Как чистая альтернатива строжке с помощью угольной дуги, плазменная строжка применяется для исключения дефектов сварных швов или поверхностных дефектов конструкционных и высоколегированных сталей. Поскольку поверхность, подготовленная под сварку, получается гладкой, нет необходимости выполнять обработку абразивом. Подводится малое количество теплоты, и поводки практически отсутствуют. Оператор без затруднения может видеть, что он или она делает. Шум и дым, которые сопровождают плазменную строжку, намного меньше, чем в случае строжки с помощью угольной дуги.
Используется для маркировки вырезаемых деталей
При выполнении маркировки изделий с помощью плазменной струи изделие подвергается нагреву, что может привести к изменению внешнего вида поверхности, так как при тепловом воздействии происходит образование цветов побежалости. (Плазменная машина не производит независимого переключения на более высокую силу тока, запуская тем самым процесс резки.) Сила тока дуги имеет максимальную величину 10 ампер. В качестве плазменных газов обычно применяются аргон, азот или воздух.
Используется для определения положения следующих деталей.
При разметке изделия плазменной струёй это изделие подвергается небольшой механической нагрузке, в результате чего на поверхности создаются выемки.
Используется для определения положения следующих деталей.
При пробивке изделия плазменной струёй это изделие подвергается небольшой механической нагрузке. Однако плазменный резак не передвигается по изделию, а плазменная струя направляется на его поверхность только на короткий период времени (около 1 сек.). (Плазменная машина не производит независимого переключения на более высокую силу тока, запуская тем самым процесс резки.) Сила тока дуги имеет максимальную величину 25 ампер. В качестве плазменного газа обычно применяют аргон или воздух.
Отправить ответ