Способ обработки металлов давлением при получении проволоки
Содержание:
Процесс обработки металлов давлением (ОМД) – это придание материалу требуемой формы, размеров, физико-механических свойств без нарушения его сплошности путем пластической деформации. Обработка металлов давлением основана на их способности в определенных условиях пластически деформироваться в результате воздействия на деформируемое тело (заготовку) внешних сил. Нарушение сплошности строения материала деформируемой заготовки в большинстве случаев недопустимо и приводит к браку.
а — прокатка; б — прессование; в — волочение;
г — ковка; д — штамповка; е — вытяжка
Рисунок 13 — Схемы основных видов обработки металлов давлением
Процессы обработки металлов давлением по назначению подразделяют на два вида:
1) для получения заготовок постоянного поперечного сечения по длине (прутков, проволоки, лент, листов), применяемых в строительных конструкциях или в качестве заготовок для последующего изготовления из них деталей только обработкой резанием или с использованием предварительного пластического формоизменения. Основными разновидностями таких процессов являются прокатка (рис. 13 а), прессование (рис. 13 б) и волочение (рис. 13 в).
2) для получения деталей или заготовок (полуфабрикатов), имеющих приближенно формы и размеры готовых деталей и требующих обработки резанием лишь для придания им окончательных размеров и получения поверхности заданного качества. Основными разновидностями таких процессов являются ковка (рис. 13 г) и штамповка (рис. 13 д).
Прокатное производство. Прокатке подвергают до 90% всей выплавляемой стали и большую часть цветных металлов. При прокатке металл пластически деформируется вращающимися валками. Взаимное расположение валков и заготовки, форма и число валков могут быть различными. Выделяют три основных вида прокатки: продольную, поперечную и поперечно-винтовую.
При продольной прокатке (рис. 13 а, 14 а) заготовка 2 деформируется между двумя валками 1, вращающимися в разные стороны, и перемещается перпендикулярно к осям валков. При поперечной прокатке (рис. 14 б) валки 1, вращаясь в одном направлении, придают вращение заготовке 2 и деформируют ее. При поперчно-винтовой прокатке (рис. 14 в) валки 1 расположены под углом и сообщают заготовке 2 при деформировании вращательное и поступательное движения.
Для нормального протекания процесса, особенно для его начала в период захвата, необходима определенная величина сил трения. Со стороны валков на заготовку действуют нормальные силы Nи сила тренияT. Для обеспечения захвата заготовки валками необходимо, чтобы тангенс угла захвата был меньше коэффициента трения. При горячей прокатке стали гладкими валками угол захвата равен 15-24°, при холодной – 5-8°.
Рисунок 14 — Схема основных видов прокатки
Таким образом, степень обжатия заготовки при прокатке в значительной степени определяется углом захвата или коэффициентом трения между валками и заготовкой. Для его увеличения часто на поверхность валков наносят риски, рифления, специальные наплавочные валики, повышая тем самым допустимую величину абсолютного обжатия.
Инструментом прокатки являются валки, которые могут быть гладкими для проката листов, полос либо с фигурными вырезами – ручьями. Совокупность соответствующих вырезов в верхнем и нижнем валках образует калибр. Пара валков обычно имеет несколько калибров.
Форму поперечного сечения продукции, получаемой при прокатке, называют профилем. Совокупность форм и размеров профилей, получаемых прокаткой, называютсортаментом (рис. 15).
Хотя сортамент прокатных изделий весьма обширен, все же представляется возможным весь прокат разбить на следующие основные четыре группы: сортовой, листовой, трубы, специальные виды проката (бандажи, колеса, периодические профили и пр.). Наиболее разнообразной является группа сортового проката, который подразделяется на простые и фасонные профили. Прокат в виде круга, квадрата, полос плоского сечения относится к простым профилям. Прокат сложного поперечного сечения относится к фасонным профилям.
Рисунок 15 — Разновидности профилей проката
В зависимости от назначения фасонные профили подразделяются на профили общего или массового потребления (угловой профиль, швеллеры, двутавровые балки, шестигранные профили и др.) и профили специального назначения (рельсы железнодорожные широкой и узкой колеи, рельсы трамвайные, профили сельскохозяйственного машиностроения, электропромышленности, нефтяной промышленности и др.). В прокатных цехах производят более 1600 размеров простых профилей, более 1100 фасонных профилей общего потребления и примерно 1350 размеров профилей специального назначения.
Волочение металла— это процесс протягивания прутка через отверстие, размеры которого меньше, чем исходные размеры прутка. При этом длина прутка увеличивается, а поперечное сечение приобретает форму отверстия с одновременным уменьшением поперечного сечения. Волочение выполняется тяговым усилием, приложенным к переднему концу обрабатываемой заготовки. Волочение производят в холодном состоянии. Данным способом получают проволоку всех видов, прутки с высокой точностью поперечных размеров и трубы разнообразных сечений.
Основной инструмент при волочениисплошных профилей –волокиразличной конструкции, а при волочении полых профилей – волоки и оправки к ним. Волочение осуществляют на волочильных станах, состоящих из тянущего устройства и волочильного инструмента.
Обработка металла волочением находит широкое применение в металлургической, кабельной и машиностроительной промышленности. Волочением получают проволоку с минимальным диаметром 0,002 мм, прутки диаметром до 100 мм, причем не только круглого сечения, трубы главным образом небольшого диаметра и с тонкой стенкой. Волочением обрабатывают стали разнообразного химического состава, прецизионные сплавы, а также практически все цветные металлы (золото, серебро, медь, алюминий, и др.) и их сплавы. Изделия, полученные волочением, обладают высоким качеством поверхности и высокой точностью размеров поперечного сечения. Если изделию требуется придать в основном эти характеристики, то такой вид обработки называют калибровкой.
Волочение выгодно отличается от механической обработки металла резанием (строганием), фрезерованием, обточкой и прочее, т. к. при этом отсутствуют отходы металла в виде стружки, а сам процесс заметно производительнее и менее трудоемок. Волочением можно изготовлять полые и сплошные изделия часто сложного поперечного сечения, производство которых другими способами не всегда представляется возможным (например, тонкие изделия, прутки значительной длины). При волочении ряда профилей (квадратный, треугольный, шестиугольный) используют составные волоки, которые отличаются высокой универсальностью, т. к. в одной и той же волоке, меняя профиль отверстия соответствующей перестановкой отдельных пластин, можно получать различные размеры профиля. Кроме составных волок при производстве прутков и главным образом труб применяют шариковые и роликовые волоки. При получении профилей сложной формы применяют дисковые волоки, в которых рабочие поверхности волочильного канала образуются поверхностями свободно вращающихся дисков (неприводных валков-роликов).
В качестве исходного материала для волочения применяют катаную и прессованную заготовки. При производстве алюминиевой, медной и другой проволоки в качестве исходной заготовки используют катанку, получаемую непосредственно из плавильной печи через кристаллизатор и непрерывный прокатный стан. Независимо от способа получения исходная заготовка перед волочением проходит тщательную предварительную подготовку, которая заключается в проведении того или иного вида термической обработки, удалении окалины и подготовке поверхности для закрепления и удержания на ней смазки в процессе волочения. Эти предварительные операции обеспечивают нормальное выполнение пластической деформации в волочильном отверстии, способствуют получению высокого качества поверхности изделия, уменьшают усилие и энергию на волочение и снижают износ волочильного инструмента.
При производстве проволоки и прутков волочением большое внимание уделяют подготовке поверхности продукта обработки перед волочением. Удаление окалины в калибровочных и волочильных цехах производят механическим, химическим и электрохимическим способами, а также комбинациями этих способов.
Прессование металла— это процесс выдавливания металла из контейнера через одно или несколько отверстий в матрице с площадью меньшей, чем поперечное сечение исходной заготовки. При прессовании реализуется одна из самых благоприятных схем нагружения, обеспечивающая максимальную пластичность — всестороннее неравномерное сжатие.
Этот способ пластической обработки находит широкое применение при деформировании как в горячем, так и в холодном состоянии металлов, имеющих не только высокую податливость, но и обладающих значительной природной жесткостью, а также в одинаковой мере применим для обработки металлических порошков и неметаллических материалов (пластмасс и др.).
Прессованием изготовляют прутки диаметром З. 250 мм, трубы диаметром 20 — 400 мм при толщине стенки 1,5 — 12 мм, полые профили с несколькими каналами сложного сечения, с наружными и внутренними ребрами, разнообразные профили с постоянным и изменяющимся (плавно или ступенчато) сечением по длине. Профили для изготовления деталей машин, несущих конструкций и других изделий, получаемые прессованием, часто оказываются более экономичными, чем изготовляемые прокаткой, штамповкой или отливкой с последующей механической обработкой. Кроме того, прессованием получают изделия весьма сложной конфигурации, что исключается при других способах пластической обработки.
К основным преимуществам прессования металла относятся: возможность успешной пластической обработки с высокими вытяжками (в том числе малопластичных металлов и сплавов); возможность получения практически любого поперечного сечения изделия, что при обработке металла другими способами не всегда удается; универсальность применяемого оборудования, позволяющего легко переходить на производство профилей различных конфигураций; производство изделий с высокими качеством поверхности и точностью размеров поперечного сечения, что во многих случаях превышает принятую точность при пластической обработке металла другими способами (например, при прокатке).
К недостаткам получения изделий прессованием следует отнести: повышенный расход металла на единицу изделия из-за существенных потерь в виде пресс-остатка; появление в некоторых случаях заметной неравномерности механических и других свойств по длине и поперечному сечению изделия; сравнительно высокую стоимость прессового инструмента.
Процесс прессования выполняется в условиях равномерного всестороннего сжатия металла, что положительно сказывается на увеличении его пластичности. Поэтому прессованием можно обрабатывать металлы и сплавы с низкой природной пластичностью. Однако трехосное сжатие вызывает необходимость значительных усилий при обработке. Поэтому прессование требует повышенного расхода энергии на единицу объема деформируемого тела. В качестве силового агрегата для прессования наибольшее распространение получили гидравлические прессы с усилием прессования 1000-1500 т. Они не боятся перегрузки, позволяют регулировать в широких пределах скорость перемещения силового плунжера, легко автоматизируются, в том числе с помощью систем программного управления.
Производство бесшовных и сварных труб. Трубы подразделяют на бесшовные и сварные. Бесшовные трубы прокатывают диаметром 30-650 мм с толщиной стенки от 2 до 160 мм, сварные – диаметром от 5 до 2500 мм. Материалом для производства труб могут быть как углеродистые, так и легированные стали, цветные металлы. В качестве заготовки для производства бесшовных труб применяют круглые или граненые слитки, а также круглые катаные прутки большого диаметра. Основной операцией является прошивка заготовки, т.н. получение в заготовке сквозного отверстия. Перед прошивкой заготовку нагревают в методической печи до температуры горячей обработки давлением и направляют на прошивочный стан с двумя бочкообразными валками, оси которых расположены под углом 10-15° друг к другу. Таким образом, при прошивке отверстия используется принцип поперечно-винтовой прокатки. В результате вращательно-поступательного движения заготовки при достаточно большой степени обжатия в центре заготовки возникают весьма значительные радиальные растягивающие напряжения, вызывающие течение металла от центра к периферии. Металл в центре доводится до состояния разрыхления, и заготовка легко прошивается неподвижным прошвинем, надвигаясь на него в результате поступательного движения заготовки. Прокатка производится несколько раз; каждый раз трубы вместе с оправкой поворачиваются в валках на 90°. Способ позволяет получать трубы диаметром 57-426 мм с толщиной стенки 3-30 мм.
Сварные трубы из низкоуглеродистых и низколегированных сталей изготавливают из прокатных полос, называемых штрипсами, или листов, ширина которых равна длине диаметра (или половине диаметра трубы). Процесс производства трубы включает в себя формовку плоской заготовки в трубу, сварку (печную, электрическую, газовую), правку, калибровку.
Печной сваркой получают трубы небольшого диаметра до 10-114 мм и толщиной 2-5 мм из низкоуглеродистой стали. Процесс включает в себя нагрев полос в газовой печи до 1300-1350°C, формовку нагретого участка в сварочной воронке и обжатие со значительной пластической деформацией. Большое распространение при производстве труб большого диаметра для магистральных трубопроводов получил способ с применением электросварки под флюсом.
Производят сварные трубы с прямыми и спиральными швами. По первой технологии из листа формируют трубную заготовку, затем ее сваривают с наложением наружного и внутреннего швов. При производстве труб со спиральным швом в качестве исходной заготовки используют ленту, которую сворачивают по спирали в трубу нужного диаметра и затем сваривают по кромке наружным и внутренним швами. Прочность, а главное надежность, труб со спиральным швом выше, чем с прямым.
Объемная штамповка –вид обработки металлов давлением, при котором формообразование поковки осуществляется пластическим деформированием заготовки в специальном инструменте – штампе. Полости в верхней и нижней частях штампа называютручьями штампа. Течение металла в штампе ограничивается поверхностями полости штампа, и в конечный момент штамповки при смыкании они образуют единую замкнутую полость, соответствующую по конфигурации штамповке.
Исходным материалом для горячей объемной штамповки служат прокатанные или прессованные прутки круглого, квадратного или прямоугольного сечения, а также периодический прокат. Штамповку можно вести непосредственно от прутка с последующим отделением его от штампованной части, однако чаще предварительно от прутка отрезают мерные куски. Штамповке подвергают чаще всего углеродистые или низколегированные стали, реже цветные металлы и сплавы. Основными достоинствами горячей объемной штамповки являются: высокая производительность (до сотен поковок в час); меньшие припуски и допуски, чем при ковке (это приводит к упрощению механической обработки и снижению ее трудоемкости); квалификация штамповщика может быть существенно меньшей, чем кузнеца.
Процесс штамповки выполняется в зависимости от вида поковки, рода материала и характера производства на установках различного вида. Наиболее широкое распространение получила штамповка на молотах, прессах, горизонтально-ковочных машинах и другом оборудовании. Молоты представляют собой машины динамического действия на обрабатываемый металл и чаще всего характеризуются массой падающих частей.
В зависимости от типа штампа горячую объемную штамповку подразделяют на штамповку в открытых штампах, штамповку в закрытых штампах и в штампах для выдавливания.
К листовой штамповкеотносятся методы получения деталей и изделий, для которых в качестве исходной заготовки используют листовой материал, трубные заготовки, катаные и гнутые профили. Листовую штамповку осуществляют как в холодном, так и подогретом состоянии. Горячей листовой штамповкой получают крупногабаритные детали паровых и гидравлических турбин большой мощности, детали прессов, прокатных станов и другие.
Процесс пластической деформации различного металла, для придания заготовке нужной формы и необходимого размера, называется обработкой металла давлением или ОМД.
Под такую обработку могут попадать только пластичные материалы типа сталь, сплавы меди, магния, алюминия и др., при этом они могут быть холодными или нагретыми.
Давление как способ обработки металла
Под давлением холодный металл деформируется, сплющивается и вытягивается. При этом он становится прочнее и тверже, но теряет пластичность и вязкость. Пластическая деформация увеличивает прочность материала, этот процесс называется наклёп.
При увеличении плотности дислокаций и высокой концентрации точечного дефекта в наклёпе, уменьшается свободное перемещение дислокаций и усложняется дальнейшее пластическое деформирование.
Обрабатывая разогретый металл, получаем увеличенную пластичность, за счёт уменьшения сопротивления. Даже небольшой нагрев уменьшает наклёп, благодаря частичному исчезновению дефектов решётки, при сохранении деформированной формы зерна. Этот эффект называется возврат металла.
Если сильнее разогреть материал, то наклёп полностью пропадёт. Начнётся процесс, при котором деформированные старые зёрна образовывают новые, более совершенные, происходит первичная рекристаллизация. Дальнейший нагрев даётвторичную рекристаллизацию, при котором увеличиваются отдельные зёрна.
Каждый сплав металла, при горячей обработке, имеет два предела — верхний и нижний. Верхняя предельная точка не доходит до линии солидуса (температура плавления) примерно 160−200 °C, а нижняя точка — на 60−70 °C больше температуры, при которой перлит и цементит превращается аустенит.
Зону пережога отделяет от перегрева всего лишь 100 °C, что очень важно, так как пережжённая деталь никуда не годна, она идёт на переплавку. Зона перегрева отличается интенсивным ростом зерна, что делает металл непрочным и хрупким. Чтобы исправить последствия перегрева, необходимо измельчить зерно, для этого применяют термическую обработку — отжиг.
Для получения наименьшего размера зерна, необходимо деформировать материал при наименьшем нагреве, когда температура близка к зоне наклёпа.
Для разогрева заготовок используют пламенные или электрические печи:
Нагрев проводят быстро и равномерно. Это минимизирует термическое напряжение и не даёт вырасти крупному зерну.
Прокат металла
Деформирование происходит во время прокатки заготовки между вращающихся валов. Давление валов уменьшает толщину металла, делая его длиннее и шире. Прокатка используется для обработки стали, цветных металлов и сплавов.
Продольная прокатка — при этой обработке заготовка движется поступательно, перпендикулярно валкам, которые движутся в разные стороны и деформируют её в длину. Такой способ используется для изготовления 90% листового и профильного проката.
Поперечная прокатка — заготовка не движется вперёд, крутиться на одном месте. Движение ей придают валки, двигающиеся в одном направлении, деформирующие круглую заготовку в поперечном сечении. Такой вид прокатки применяют для производства валов, зубчатых колёс.
Поперечно-винтовая прокатка — заготовка получает вращательно-поступательное движение от перекошенных валков, расположенных под углом и вращающихся в одном направлении. Металл деформируется одновременно вдоль и поперёк. Такой вид проката используют для изготовления бесшовных труб.
Прокатные валки
На производство прокатных валков идёт легированная сталь или высокопрочный чугун. У каждого валка есть рабочая часть — так называемая бочка, шейка и трефа. Шейка предназначена для вращения в подшипнике, а трефа необходима для соединения валка с муфтой или шпинделем, чтобы получать от них крутящий момент.
Валок может быть гладким или калиброванным, для получения определённого вида проката. Прокат осуществляется на прокатном стане.
Прокатный стан
Прокатные станы разделяются на двух, трёх и многовалковые. Они могут быть со стационарным реверсивным или нереверсивным направлением вращения валов, и с изменяемым направлением вращения валов.
Прокатный стан может быть:
обжимным;
- сортовым;
- листовым;
- рельсовым;
- трубопрокатным и др.
Отличаются станы и по размеру, бывают мелко и крупносортные. Крупносортный стан — называется блюмингом либо слябингом. Они предназначены для проката больших слитков в квадратную заготовку — блюм или в прямоугольную — сляб.
Прокатное производство выпускает не только готовую продукцию (трубы, проволока, арматура, рельс), также это заготовки для дальнейших механических обработок. Профиль производственного проката может быть листовым, сортовым, трубным и специальным.
Листовой:
- Тонколистовой прокат металла толщиной менее 4 мм. При толщине листа меньше 0,2 мм это будет фольга или жесть.
- Толстолистовой прокат листа более 4 мм и до 160 мм. Такие изделия получают только при разогретой обработке.
Сортовой:
- Простой прокат — круг, квадрат, прямоугольник, квадрат и т. д.
- Фасонный прокат — тавр, двутавр, уголок, рельс, швеллер.
Трубный:
Для этого изобрели сложный технологический трубопрокатный стан. Трубный прокат даёт возможность получать бесшовную и сварную горячекатаную трубу.
Волочение металла
Холодная заготовка металла протягивается через суживающееся отверстие, это происходит под большим давлением. Такое отверстие называется — волока. Волочение делают, проводя заготовку через несколько отверстий с уменьшением диаметра. Во время этого процесса происходит наклёп. Чтобы снять прочность материала, делают отжиг и травление окалины.
Проволока, калиброванный прут, тонкостенная труба различного профиля — получаются благодаря применению волочения. Продукция выходит точного размера и с чистой поверхностью.
Для того чтобы волока выдерживала жёсткие условия использования, на её изготовление идёт инструментальная сталь или твёрдый металлокерамический сплав, на производстве тонкой проволоки применяются технические алмазы.
Чтобы уменьшить трение, отвести тепло и повысить стойкость инструмента применяется жидкая и сухая смазка. Это может быть различное минеральное масло, эмульсия, мыло или графитовый, медный, молибденовый порошок.
Прессование заготовки
Прессование — это горячая обработка металла давлением. Используя всестороннее сжатие и давление, разогретый металл выдавливается через отверстие в матрице. Для металлов с низкой пластичностью, такая обработка считается единственным методом, дающим возможность получить прут с простым или сложным сечением.
Прессование может быть двух методов:
При этом меняется только движущая часть пресса. В первом случае — движется пуансон к заготовке, во втором — заготовка к пуансону. Для получения прута любого сечения можно использовать любой метод прессования, а трубы можно получить только благодаря прямому прессованию.
Условия работы пресс-камеры, пуансона и пресс-шайбы очень жёсткие. Благодаря большому давлению и высокой температуре они быстро приходят в негодность. Их изготавливают из жаропрочных сплавов и инструментальной стали.
Чтобы увеличить срок службы используют смазывающие вещества: минеральное масло, графит, канифоль, в определённых ситуациях применяется жидкое стекло. Этот метод обработки имеет недостаток — необрабатываемый остаток, около 20% металла остаётся в прессе.
Ковка металла
Обработка металла при помощи молота или пресса. Деформирование происходит между двух плоскостей. Такое изделие называется поковка. Низкая производительность сопутствует ручной ковке, поэтому в промышленности используют машинную ковку.
Во время ковки, металл неограничен рабочей поверхностью и может растекаться по сторонам инструмента. У молота или пресса есть два бойка, нижний и верхний. Первый — неподвижный, второй подвижный, заготовку помещают между ними.
Ковка может нести основной и вспомогательный характер.
Осадка — уменьшается высота заготовки, при этом увеличивается площадь поперечного сечения.
- Высадка — осаживается часть заготовки. Для этого используют оправку — подкладной инструмент.
- Протяжка — увеличивается длина заготовки, за счёт уменьшения площади поперечного сечения.
- Раскатка при помощи оправки — увеличивается внутренний и наружный диаметр кольца, постепенно уменьшая толщину стенок.
- Прошивка — получение сквозного отверстия. Используют прошивень, благодаря ему делают и полость. Отходы металла называют выдра.
- Рубка — отсоединение некоторой части заготовки.
- Гибка — придание заготовке изгиба, используя заданный контур. Благодаря опорам и приспособлениям делают различные угольники, скобы.
- Скручивание — часть заготовку проворачивают вокруг своей оси.
- Передача — вертикально смещается часть заготовки по отношению к другой её части. Используются дополнительные опоры.
Штамповка формовая
Изготовление сложного изделия, используя давление и специальную форму — штамп. Штамповка бывает объёмной или листовой, может проводиться с горячей или холодной заготовкой.
Металл для объёмной штамповки имеет простую форму, а деформируясь, заполняет полость всего штампа. Листовая штамповка незначительно изменяет толщину получаемой детали от первоначальной толщины заготовки. Чаще всего, объёмную штамповку проводят с разогретым металлом, а листовую с холодным. Горячая листовая штамповка проводится в случаях, когда необходимо обработать давлением металл, который будучи холодным, недостаточно пластичный.
Горячая
Используя горячую объёмную штамповку, благодаря специальным штампам, из заготовки производят штампованную поковку. Штамп — так называют форму будущей детали, в которую впрессовывается заготовка. Он состоит, как правило, из двух деталей: первая часть крепится неподвижно к молоту или прессу, вторая — к подвижной части оборудования. Между ними, для выхода лишнего металла, предусмотрены полости — ручьи.
Существует две разновидности штампа:
- Открытый — специально создан зазор между половинками штампа, для выхода избытка металла — облой или заусенец. Он закрывает выход, этим способствует заполнению металлом всей формы.
- Закрытый — зазор между частями штампа отсутствует. Нет отходов, минимальный расход и улучшенная структура металла в изделии. Требует очень точного измерения массы заготовки.
Отличается штамповка одноручьевым и многоручьевым штампом.
Одноручьевой штамп — это одна полость. Используются для штамповки изделий простых конфигураций.
Многоручьевой штамп — сложные, несколько уровневые изделия. Заготовка проходит первоначальную деформацию за счёт черновых ручьёв, это вытяжка или гибка. Следующий этап, окончательная придача формы, используя штамповочные ручьи.
Для приготовления штампов используется легированная сталь и специальная штамповочная сталь, у которой высокая твёрдость, вязкость и жаропрочность.
В качестве оборудования используется газовоздушный штамповочный молот или гидравлический пресс.
Холодная
Эта штамповка обладает высокой производительностью и низкой себестоимостью. Это хорошая возможность получить простые или сложные детали с высокой точностью выполнения.
Холодное выдавливание — формируется сплошное или полое изделие, используется пластическое течение металла, через одно или несколько отверстий штампа. Этот метод деформирования имеет похожие с прессованием черты. Металл может выдавливаться через различные отверстия, соответственно выдавливание может быть прямым, обратным и комбинированным.
- Холодная высадка — саживается часть заготовки. Этот способ применяют в производстве различных крепёжных изделий. Холодную объёмную штамповку производят одинаково с горячей, только используют открытые штампы.
- Отрезка — операция с целью холодного отделения некоторой части листа, используя штамп или машинные ножницы.
- Вырубка, пробивка — отсоединяется часть заготовки в замкнутом контуре. В первой ситуации вырубаемая часть — необходимая деталь, во второй — отходы.
- Правка— формирующая операция необходимая для удаления неровности и кривизны плоских поверхностей.
- Вытяжка — деформация листа до пустотелой выпуклости, открытой с другой стороны.
- Гибка — придание заготовке необходимой кривизны.
- Отбортовка — придание предварительно выбитым отверстиям вида горловины или борта.
- Обжим — уменьшение диаметра концевой части полой заготовки.
- Вальцовка — применяется для получения трубы из листового металла или чтобы получить гофрированную поверхность.
- Взрывная штамповка — листовую заготовку устанавливают на матрицу и опускают под воду, масло или песок, а над промежуточной средой производят взрыв. Энергия от взрыва передаётся заготовке и деформирует её согласно матрице. Если пропускают через воду электрический разряд, то получают подобную ударную волну, а процесс называют электрогидравлической штамповкой.
Ещё существует специализированная обработка давлением, к ней относится: обкатка, раскатка и калибровка отверстий, накатка рифлений, резьбы и зубьев.
Обкатку и раскатку используют, чтобы упрочнить любую поверхность детали. Будь она плоской, конической или цилиндрической формы, снаружи и внутри её.
Калибровку проводят специальным шариком или стержнем, путём одноразового или многократного перемещения инструмента. При многократной калибровке используют увеличивающийся размер инструмента, что сглаживает неровности и упрочняет поверхность.
Накатку используют при необходимости получить фасонную поверхность, ту же резьбу, клейму, рифление на плоскости и др. Для этого вдавливают необходимый инструмент в заготовку.
В результате ОМД можно получить готовые изделия практически любой формы, всевозможных размеров и параметров. Это стало возможным благодаря современным технологиям. Подобная продукция востребована во всех сферах деятельности человека и с каждым днём становится ещё более необходимой.
МЕТОДЫ получения и обработки материалов и изделий
Получение изделий методом литья
Литьё − это способ изготовления заготовки или изделия заполнением полости заданной конфигурации жидким металлом с последующим его затвердеванием. Различают слитки и отливки. Для литья слитков используют деформируемые сплавы, а для литья отливок — литейные.
Слитки, как правило, изготавливаются круглыми или плоскими. Они имеют большую массу и значительные габаритные размеры. Слитки используют для получения деталей машин и другой металлической продукции методами пластического деформирования (рис. 1).
![]() |
![]() ![]() |
Рис. 1 — Слитки, полученные методом литья
Исходная заготовка — слиток (схема А) — в процессе изготовления конкретных деталей многократно подвергается нагреву до довольно высоких температур (до tнагр=0,7tпл) с одновременным силовым воздействием на металл, которое последовательно изменяет форму исходной заготовки, приближая ее к конфигурации требуемой детали (фасонная заготовка).
В результате теплового и силового воздействия структура металла претерпевает существенные изменения, часть литейных дефектов исчезает, механические свойства металла существенно повышаются.
![]() |
Схема А: кузнечно-штамповочное производство (из слитков) |
Отливки получают методами фасонного литья. Конфигурация отливок максимально приближена к размерам и конфигурации готовой детали. Методами фасонного литья можно изготовить детали практически любого веса (от несколько грамм до сотен тонн), любого размера (от миллиметров до нескольких метров), любой сложной конфигурации (рис. 2).
![]() |
![]() |
![]() |
Схема Б: литейное производство (из отливок) |
Литейная форма представляет собой систему элементов, образующих рабочую полость с внешними контурами получаемой отливки.
· Разовая форма — получения отливки разрушают. Форма изготовляются путем уплотнения формовочных смесей, основой которых является кварцевый песок.
· Постоянная форма — пригодная для многократного применения.
Выбор способа литья определяется:
· служебным назначением детали,
· требуемой точностью и качеством поверхности отливки.
Виды литья подразделяют на (рис. 3):
· литьём в песчаные формы | Распространенный метод литья |
· ![]() |
Специальные виды литья, когда качество отливки не удовлетворяет предъявляемым требованиям − высокая точность, − лучшее качество поверхности, − меньшие величины припусков |
|
а) Литьё в песчаные формы
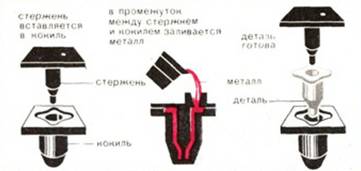
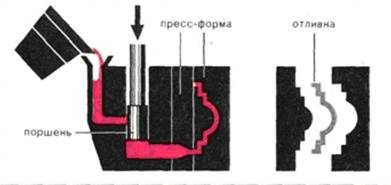
Рис. 3. Виды литья
Эффективность литья может быть оценена через коэффициент использования металла (КИМ) — отношение масс детали и заготовки.
Виды деформированного полуфабриката
Требования к литейным материалам:
— отсутствие различного рода дефектов (трещины, спаи, пригары, заливы)
Жидкотекучесть − это способность металлов и сплавов занимать литейную форму. Чистые металлы и сплавы эвтектического состава обладают лучшей жидкотеучесть, чем сплавы-твёрдые растворы, доэвтектические и заэвтектические сплавы.
Раковинывнутренние или наружныепустоты в теле отливки. Они могут быть пустыми или заполнены формовочным материалом, шлаком. С гладкой или шероховатой поверхностью. По природе происхождения различают: усадочные, газовые, шлаковые, песчаные.
Дефекты литья(пригары, спаи, заливы) — образуются в результате нарушения технологических параметров литья
![]() |
![]() |
а) жидкотекучесть | б) усадочная раковина |
![]() |
![]() |
в) горячая трещина | г) поры в слитке |
Рис. 4 — Дефекты литья
Пластическая деформация (ПД)
Характерной особенностью металлов и сплавов является способность непрерывно деформироваться вплоть до разрушения под воздействием внешних сил, приложенных к металлу. Процесс деформации складывается из упругой и пластической деформаций и завершается разрушением.
Упругая (обратимая)деформация — это деформация, которая полностью исчезает после снятия нагрузки.
Пластическая (необратимая)деформация характеризуется остаточной деформацией в металле после снятия нагрузки. Кроме упругих напряжений она вызывает и остаточные, а также изменения в структуре металла, которые увеличиваются с ростом нагрузки вплоть до разрушения.
При пластической деформации происходит движение имеющихся дислокаций и образование огромного количества новых дислокаций в различных кристаллографических плоскостях и направлениях В недеформированном кристалле плотность дислокаций достигает 10 6 см -2 , а в сильно деформированном металле порядка 10 12 см -2 . Если на пути движения дислокаций встречается препятствие в виде другой дислокации или дефектов другого рода, то процесс движения дислокаций тормозится и необходимы более высокие внешние напряжения, чтобы продеформировать материал, т. е. происходит деформационное упрочнение (наклеп, нагартовка, упрочнение – слова синонимы). Оно проявляется в процессе деформации и сохраняется по окончании деформирования.
Таким образом, увеличение количества (плотности) дислокаций в структуре деформированного металла в процессе пластической деформации ведет к повышению прочности
Например, путем ХПД; легированием; термической обработки (создаётся структура металла, с минимальной подвижностью дислокаций).
В процессе пластической деформации изменяется структура, а следовательно, все свойства металлов и сплавов. При высоких степенях деформации в деформированных полуфабрикатах возникает волокнистая структура с определенной кристаллографической ориентировкой, называемой текстурой деформации. Возникновение волокнистой текстурованной структуры в процессе деформирования вызывает анизотропию свойств деформированного полуфабриката, что обуславливает различное поведение листового материала при глубокой вытяжке (рис. 5а). При деформировании увеличиваются прочностные характеристики (твердость, sв, s0,2) и понижаются пластичность (s, y) и ударная вязкость (КСU) (рис. 5б)
![]() |
![]() |
Рис. 5. Изменение микроструктуры (а) и механических свойств (б) металла от степени деформации
Получение изделий методом обработки металлов давлением
Обработки металлов давлением (ОМД) — это придание металлу требуемой формы, размеров и физико-механических свойств без нарушения его сплошности путем пластической деформации. ОМД подразделяется на горячую пластическую деформацию (ГПД) и холодную пластическую деформацию (ХПД).
При обработке металлов давлением на металл действуют внешние силы (удары молота, давление пресса), вызывающие в нем напряжения, превышающие предел упругости. В результате изменяется форма исходного металла, а объем его остается постоянным (не считая потерь на отходы и угар).в процессах ОМД упругая и пластическая деформация сопутствуют друг другу. При пластической деформации происходит изменение исходной структуры с резким повышением механических свойств металла.
В зависимости от температуры деформации различают холодную и горячую пластическую деформацию
Холодная пластическая деформация | Горячая пластическая деформация |
— проводят при температурах ниже tрек — приводит к наклепу металла или сплава — обработка давлением (ОД) ниже tрек называется холодной обработкой давлением | — проводят при температурах выше tрек — сопровождается рекристаллизацией Þ наклеп устраняется — обработка давлением (ОД) выше tрек называется горячей обработкой давлением |
Таким образом, границей между холодной и горячей обработкой давлением является температура рекристаллизации материала.
Холодной обработке давлением поддаются только ковкие металлы, обладающие достаточной пластичностью Например: Свинец (Pb), Олово (Sn), Алюминий (Al), Медь (Cu), Цинк (Zn).
Хрупкие металлы и сплавы обработке давлением не обрабатываются. (Например: Магний (Mg), чугун, твердые сплавы.
Металлы и их сплавы, обладающие недостаточной пластичностью, обрабатывают в горячем состоянии. Например: Титан (Ti), Стали.
Металл | tпл,°С | tрек | Вывод |
свинец (Pb) | 327° | -30 |
Обработка давлением при tкомн.
является горячей ОД
к процессам горячей деформации относят процессы, протекающие при температуре выше температуры рекристаллизации. Для проведения процессов ГПД металл необходимо нагреть выше
tнагр ³0,7×Тпл для обеспечения полного протекания разупрочняющих процессов.
Достоинства горячей пластической обработки | Недостатки горячей пластической обработки |
Нагрев металла выше tрекр приводит Þ 1. Увеличивается способность к ПД 2. Уменьшается сопротивление деформации 3. ГОД менее трудоёмкая и энергоёмкая | Наличие окалины на поверхности детали Þ 1. Хуже качество поверхности. 2. Меньшая точность геометрических размеров |
Для обработки металлом давлением важно строгое соблюдение режима нагрева, так как он оказывает влияние на качество и точность геометрических размеров полуфабриката, состояние оборудования и технико-экономические показатели производства. В процессе нагрева возникает перепад температур между внутренними и наружными зонами заготовки, которые сопровождаются возникновением термических напряжений. Они при недостаточной пластичности металла или сплава могут привести к возникновению и развитию трещин в нагреваемом полуфабриката
Процессы обработки металлов давлением по назначению подразделяют на два вида:
1. Для получения заготовок постоянного поперечного сечения по длине -прутки, проволока, листы (рис. 3 а, б, в). Разновидностями ОМД являются прокатка, прессование и волочение;
2.Для получения деталей или полуфабрикатов, имеющих приближённо формы и размеры готовых деталей (рис. 3 г,д). Разновидностями ОМД являются ковка и штамповка.
![]() |
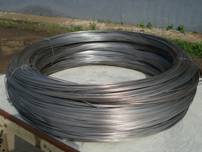
г) штампованные изделия
д) кованое изделие
Рис. 3 — Полуфабрикаты полученные методами пластической деформацией
Прокатка — процесс обжатия металла между вращающимися валками стана (рис. 4 а).
Волочение —состоит в деформации металла путем протягивания через сужающийся по длине канал круглого, квадратного или более сложного профиля. Получаемые заготовки — проволоки, прутка или трубы (рис. 4 б).
Прессование — процесс выдавливания (экструзии) находящегося в полости контейнера металла через выходное отверстие — очко матрицы (рис. 4 в).
Ковка — процесс свободного течения металла под воздействием периодических ударов или статических воздействий инструмента (необходимое изменение формы заготовки) (рис. 4 г).
Штамповка — способ изготовления фасонных заготовок пластической деформацией с помощью специального инструмента (штампов), рабочая полость которых определяет конфигурацию конечной штамповки (изделия) (рис. 4 д).
Прокатка − из плиты толщиной H получается лист толщиной h ![]() |
Волочение − из прутка диаметром D получается проволока диаметром d ![]() |
Прессование − из слитка получается длинномерный профиль (прутки) ![]() |
Ковка − из заготовки произвольной формы получается кованое изделие (подкова) ![]() |
Штамповка − из заготовки в виде листа (пунктирные линии) получается фигурный профиль ![]() |
Рис. 4. Виды обработки металлов давлением |
Оценка обрабатываемости давлением необходима при разработке новых деформируемых сплавов и при совершенствовании технологии производства и корректировки состава существующих сплавов. Обрабатываемость давлением включает сочетание оценок податливости материала и его технологической пластичности.
Податливость материала − это силовая характеристика сопротивления деформации. В случае повышенного сопротивления для обработки данного металла требуется более мощное оборудование.
Технологическая пластичность − это характеристика предельной степени деформации, после которой либо происходит локализация деформации, либо наступает разрушение металла во время обработки металла давлением в производственных условиях.
Дата добавления: 2018-08-06 ; просмотров: 113 ; ЗАКАЗАТЬ РАБОТУ
Отправить ответ