genium |
quote: Изначально написано Misantrop:
При мне из куска ножовочного быстрорезного полотна на точиле за несколько минут было сделано косое зубило, которым при мне же были срублены петли с металлических гаражных ворот
Ну а если этим полотном рубить, как мачете — что будет? Я наблюдал сломанных множество, хрупкость быстрореза термообработанного для металла общеизвестна. Особенно Р18 на максимальной твёрдости — как стекло.
Что до кованного с закалкой ниже по твёрдости — если он правится на холодную, то это совсем замечательно. Рез кстати совсем не такой, как у промышленно термообработанных.
отпуск вроде не простой, но явно выше 700 грд, т.к. предел красностойкости только до 600.
Вероятно закалка быстрореза для ножа сильно проще, чем инструментальная.
Поскольку быстрорез именуется самокалом, т.к. при остывании приобретает потребную структуру, возможно закалки после ковки нет или же она выполняется в одно действие.
самый вязкии промышленный быстрорез — на ножах для промышленной деревообработки. Но тоже точится тяжело и мылит. Кованный кобальтовый — это совершенно иное. Пробовать его согнуть я не буду. Но впечатление, что он достаточно вязкий.
Кобальт сам по себе достаточно твёрдый металл, и его функция прочного связующего проявляется и в быстрорезах.
Он ведь не образует карбидов, значит образует раствор со связующим.
Стойкость сверла по нержавейке кобальт увеличивает в несколько раз, без значимого понижения прочности его.
Аустенит — возможно и увеличивает его образование по границам зёрен, что отчасти способствует хрупкости, но а при закалке на первичную твёрдость? В справочниках описывается инструментальная то.
Нож, кованный из кобальтового быстрореза обладает великолепными свойствами — это в теме не я один утверждаю. Разобрать вопрос на более глубоком структурном уровне мы не можем.
Рекомендованные сообщения
Создайте аккаунт или войдите в него для комментирования
Вы должны быть пользователем, чтобы оставить комментарий
Создать аккаунт
Зарегистрируйтесь для получения аккаунта. Это просто!
Войти
Уже зарегистрированы? Войдите здесь.
Сейчас на странице 0 пользователей
Нет пользователей, просматривающих эту страницу.
БЫСТРОРЕЖУЩАЯ СТАЛЬ
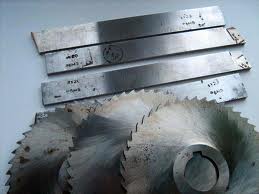
Теплостойкие стали высокой твердости, называемые быстрорежущими или быстрорезами, – группа высоколегированных инструментальных сталей, которые благодаря составу и специальным режимам термообработки на вторичную твердость имеют очень высокое иносо- и красностойкость(до 550 – 600°С). Они сочетают теплостойкость (600-700˚С) с высокой твердостью (HRC 63-70) и повышенным сопротивлением пластической деформации. В результате применениябыстрорежущих сталей стало возможным увеличить скорость резания в 2-4 раза (а более новых сталей с интерметаллидным упрочнением даже в 5-6 раз) и повысить стойкость инструментов в 10-40 и более раз по сравнению с получаемыми для инструментов из нетеплостойких сталей. Эти преимущества проявляются при резании: с повышенной скоростью, т.е. в условиях нагрева режущей кромки, или при меньшей скорости, но с высоким давлением. Для понимания особенностей свойств и области использования их важно, что снижение их твердости на HRC 2-4 по сравнению с получаемой максимальной может сопровождаться ухудшением вязкости, прочности и износостойкости. Быстрорежущая сталь необходима в использовании в состоянии высокой твердости и при работе без больших динамических нагрузок.
Теплостойкость быстрореза создается специальным легированием и закалкой с очень высоких температур: 1200-1300˚С. Основные легирующие элементы – вольфрам или вольфрам вместе с молибденом. Многочисленные быстрорежущие стали целесообразно различать по главному свойству: умеренной, повышенной и высокой теплостойкости. Стали умеренной и повышенной теплостойкости имеют относительно высокое содержание углерода (≥0,6-0,7%) и одинаковую природу упрочнения; вторичная твердость создается выделением карбидов при отпуске.
Быстрорежущая сталь умеренной теплостойкости сохраняют твердость HRC 60 после нагрева (4ч) до 615-620˚С. Они пригодны для резания сталей и чугунов с твердостью до HB 250-280, т.е. большинства конструкционных материалов, и используются наиболее широко (78-80% от общего производства быстрорежущих сталей). Характерными представителями этой группы являются стали Р18 и более рационально легированные: вольфрамовые (сталь Р12) и вольфрамомолибденовые (сталь Р6М5).
Стали повышенной теплостойкости имеют высокое содержание или углерода (азота) или же их легируют дополнительно кобальтом. Они сохраняют твердость HRC 60 после нагрева 630-650˚С. Стойкость инструментов при правильном использовании этих сталей в 1,5-4 раза выше, чем у сталей умеренной теплостойкости.
Стали высокой теплостойкости сохраняют твердость HRC 60 после нагрева 700-730˚С. Природа их упрочнения принципиально другая – за счет выделения интерметаллидов. Эти стали при правильном назначении, например для резания многих труднообрабатываемых материалов, обеспечивают повышение стойкости в 10-15 и более раз.
Маркировка быстрорежущих сталей:
Число после буквы «Р» указывает на среднее содержание вольфрама (в процентах от общей массы, буква В пропускается). Затем после букв М, Ф и К указывают процент молибдена, ванадия и кобальта.
1.Химический состав быстрорежующих сталей (ГОСТ 19265-73)
Отправить ответ